次世代のモノ作りに挑戦 第8回
株式会社KSプランニング徳島工場 副工場長 大貫 俊彦氏
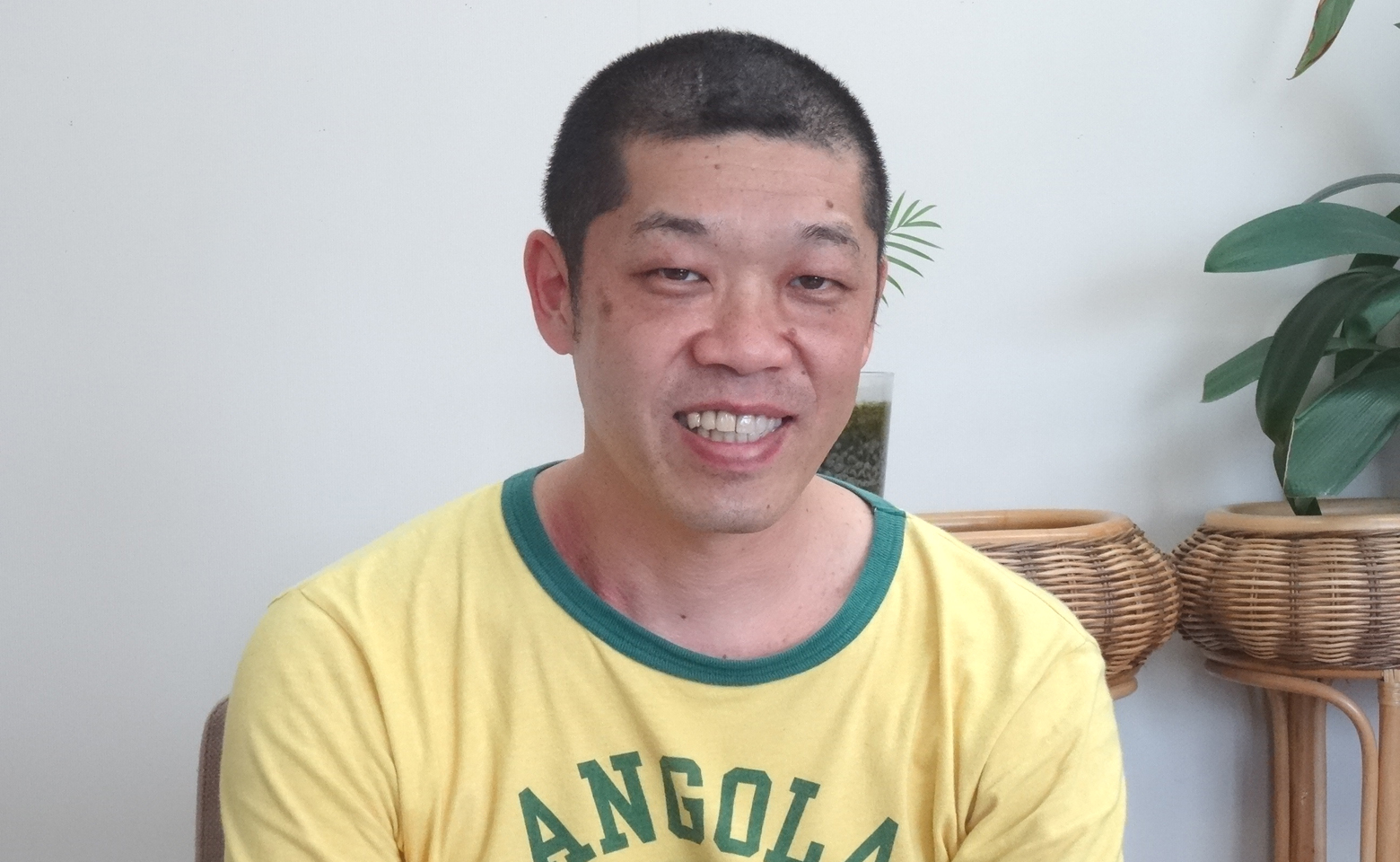
近藤紡績所(名古屋市)は、糸からの一貫生産体制を確立する紡績事業をはじめ、アパレル、小売りまで幅広い事業を展開しています。その中でアパレル事業を担うKSプランニングは、大阪・東京を拠点にして国内著名ブランド向けに企画から最終製品まで提供していますが、メイド・イン・ジャパンの製品を手掛けているのが徳島工場(徳島県板野郡藍住町)です。同工場では子供服やレディスを生産しており、効率向上のためJUKIのフルデジタル仕様・ダイレクトドライブ高速本縫い自動糸切りソーイングシステム「DDL-9000C-FMS」10台を導入、この7月から稼働しています。現場を預かる大貫俊彦副工場長に現状やデジタルミシン採用の狙いなどについてお聞きしました。
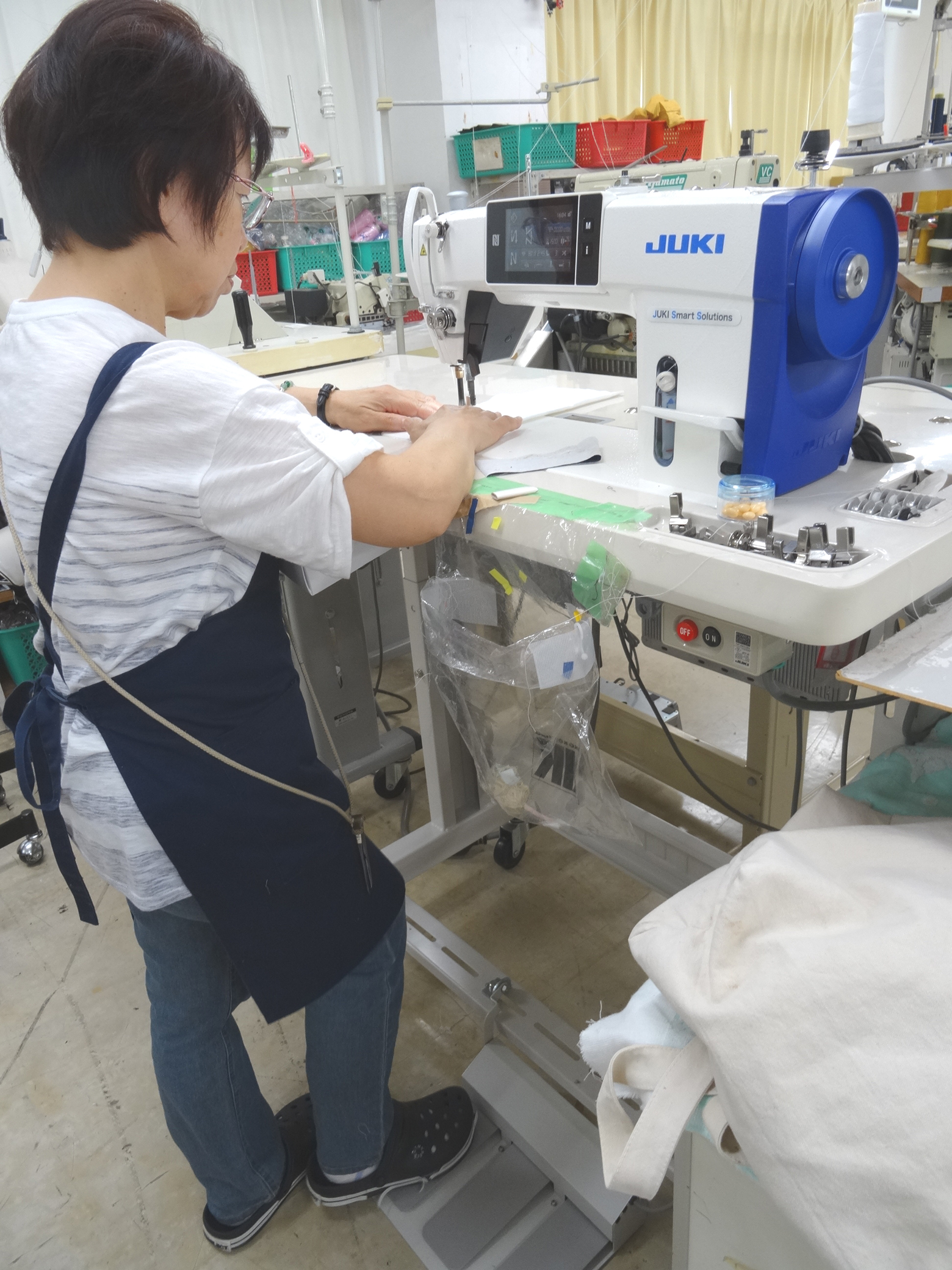
立ちミシン仕様の「DDL-9000C-FMS」10台を導入
デジタルミシンを活用しロス低減へ
ー2016年12月にKSプランニング徳島工場としてスタートしたそうですね。
近藤紡績所は素材メーカーでありながら、カジュアルブランド「ランドリー」をM&Aするなど、糸から紡績、アパレル、小売りまで事業が広がっています。会社案内のとおり国内では紡績の大町工場(長野県)があり、海外では中国、ベトナム、インドネシアに生産拠点を置いています。中国は染色から加工、縫製までを一貫して行うニット製品のOEM(相手先ブランドによる生産)拠点、ベトナム、インドネシアは綿紡績の拠点ですが、インバウンド対応を含めて国内でモノ作りをしようとすると、どうしても縫製は協力工場頼みになってしまいます。本当に糸から製品まで一貫で管理しようと思えば、やはり同じ傘下に縫製工場が必要ということで国内工場を探していたそうです。もともとここは大進繊維としてベビー、子供服を生産していましたが、縁あって近藤紡に設備と人を引き継いで頂き、2016年12月1日からKSプラニング徳島工場として再スタートを切りました。現在、近藤紡から工場長をはじめ3人が来られ、ボクは大進繊維時代からそのまま残って現場の管理を担当しています。
ー現状は。
人員は40人で、全員日本人です。平均年齢も約40歳と若く、下が高校新卒入社の2年目、上が60歳手前くらいです。もともと地元の高校とのつながりがあり、毎年新卒が2、3人入っていたのですが、さすがに徳島県も含めて日本全国で人手不足と言われているように、今年4月は残念ながらゼロでした。生産アイテムはレディスも一部ありますが、一番多いのは子供服で、カットソーのカバーオール、プルオーバー、トレーナー、Tシャツなどを1カ月に1万~1万5千着生産しています。一昨年は受注が落ち込みましたが、今年は戻ってきている感じですね。
メイド・イン・ジャパンの子供服を生産
ー近藤紡グループとしては生地から一貫提案できるのが強みになりますが。
KSプランニングは大阪と東京に営業を置き、この工場で生産している受注はどちらかと言えば子供服関係は大阪がメイン、レディス関係は東京。近藤紡の中国で作ったカットソーの生地をお客様アパレルに対して、この生地でこういうデザインでとプレゼンし、ピックアップされるという形です。約7割が近藤紡の生地になっているそうで、グループの持つ一貫体制のメリットを発揮できていると思います。徳島工場が出来たことによって、メイド・イン・ジャパンを要望されるお客様にも対応できるようになりました。特に子供服はメイド・イン・ジャパンを求められる製品が多いんです。4、5年前から「日本製」タグを付けて販売している子供服アパレルのお客様があり、最近は同じように「日本製」タグを付けられるお客様が増えています。それはインバウンド対応も意識されているからでしょう。紙おむつや粉ミルクと一緒で、来日したときに日本製ならば安心ということで買って帰られるわけです。やはり安心・安全の日本製商品に対しては高い信頼感があるんですね。
近藤紡グループで生地から一貫
ー生産現場ではどんな取り組みをしているのですか。
裁断は昨年自動裁断機(CAM)を入れ替えました。縫製現場では大進繊維時代にトヨタ生産方式「TSS」を導入し、現在もそれをベースにしたモノ作りを続けています。多品種小ロット対応にはこの生産の仕組みが一番メリットがあるということで取り入れたと聞いています。ですから現場は立ちミシンの1枚流しで、今は1ライン5~7人編成の3ラインがあり、1ラインはカバーオール、残り2ラインでトレーナーを生産しています。1枚流しなので、最初の1枚を投入してミスも早く見つけられますし、ムリ・ムダが見つけやすい、そこが一番のメリットと思います。まだ前工程の仕掛かりが多く、ボクら自体が対応し切れていないところもありますし、管理力が足らないところはありますが、やはり見てすぐ分かる管理方法というのがこの生産方式のメリットです。
ーJUKIのフルデジタル仕様本縫い自動糸切りソーイングシステム「DDL-9000C-FMS」も10台採用されています。
ちょっと古いタイプのミシンがあり、油汚れの問題も起きかねないので設備更新が必要になっていました。それで今年2月に開かれた大阪ミシンショーに行って最新のデジタルミシンを見て、これがいいと判断、本社に申請してとりあえず10台だけ買い換えさせて頂いたという経緯です。アイテムが多様ですから、ロック仕様、本縫い仕様の製品があり、カットソー工場といえどもある程度本縫いミシンが必要なんです。6月末にセットし、7月から稼働していますが、企画・サンプルに1台と、現場の3ラインに3台ずつ入れ、すべて立ちミシン仕様にしてもらいました。
ーどのように活用されていますか。
サンプル作成に入れた1台ではデジタルミシンの特色である縫いデータの収集を行っていますが、今後はこのデータの活用方法を考えて行くのがテーマです。縫製ラインに入れたミシンでは、今はトレーナーなどの袖口や裾回りにリブを縫い付けるため2本針ミシンでカバーリングステッチを入れていますが、そのステッチがほどけないようにするためこのデジタルミシンで縫い終わりに閂止めをしています。それとネーム付けの工程に使用しています。縫い終わりの糸残りをカットする手間もなくなりました。これから期待しているのが段差縫いの工程で、自動的に生地の厚みを感じて押さえ圧をデジタル管理してくれる機能があります。まだ導入したばかりで初歩段階ですが、人の手を補助してくれるような機能をどんどん使えれば、本当に安定した品質のモノ作りをしていけるし、デジタルミシンを活用してロスを減らしていきたいと考えています。
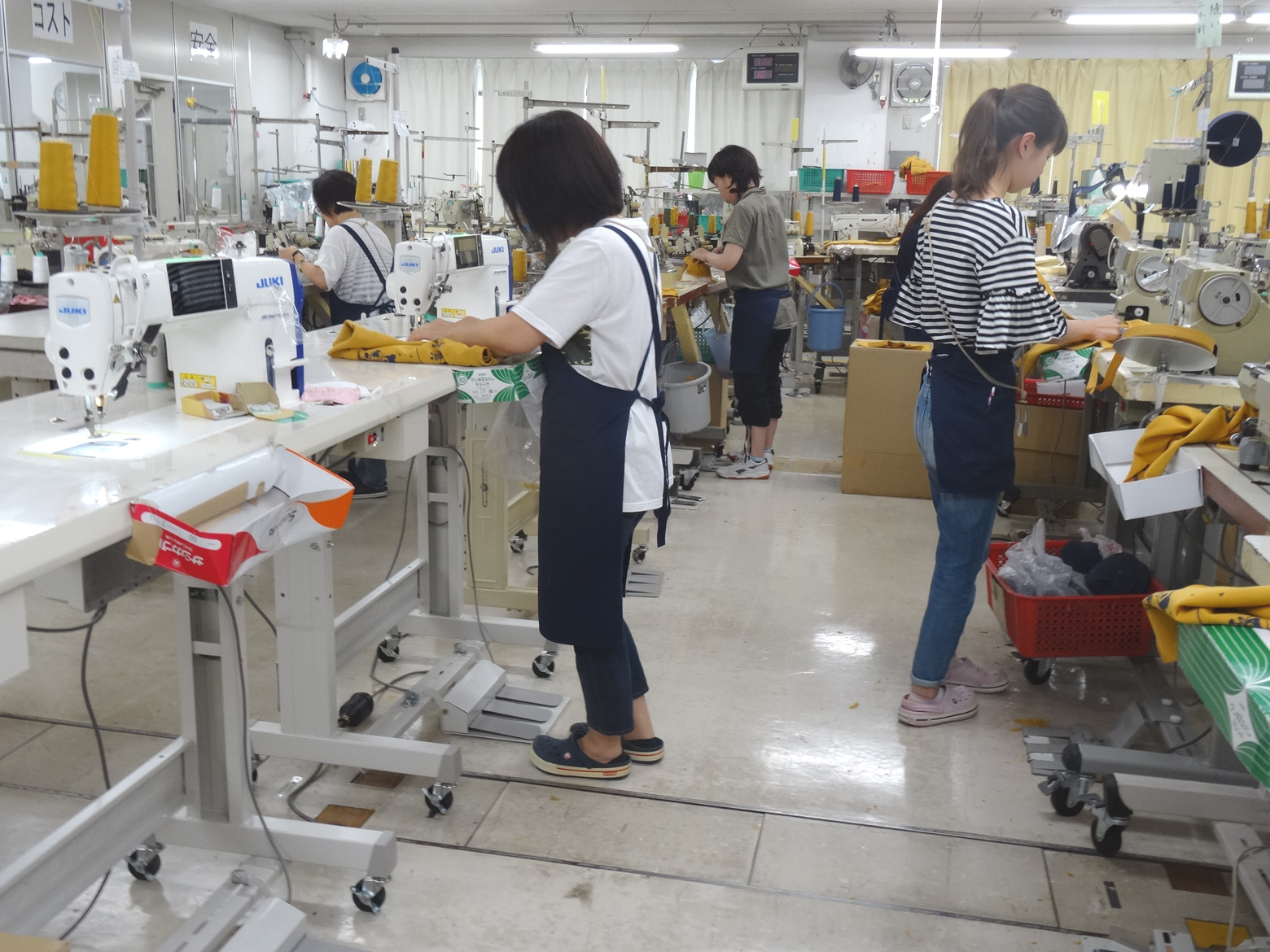
2016年12月から近藤紡グループの子供服工場としてスタート