わが社のモノ作り戦略 第22回
岩手モリヤ 代表取締役社長 森奥 信孝氏
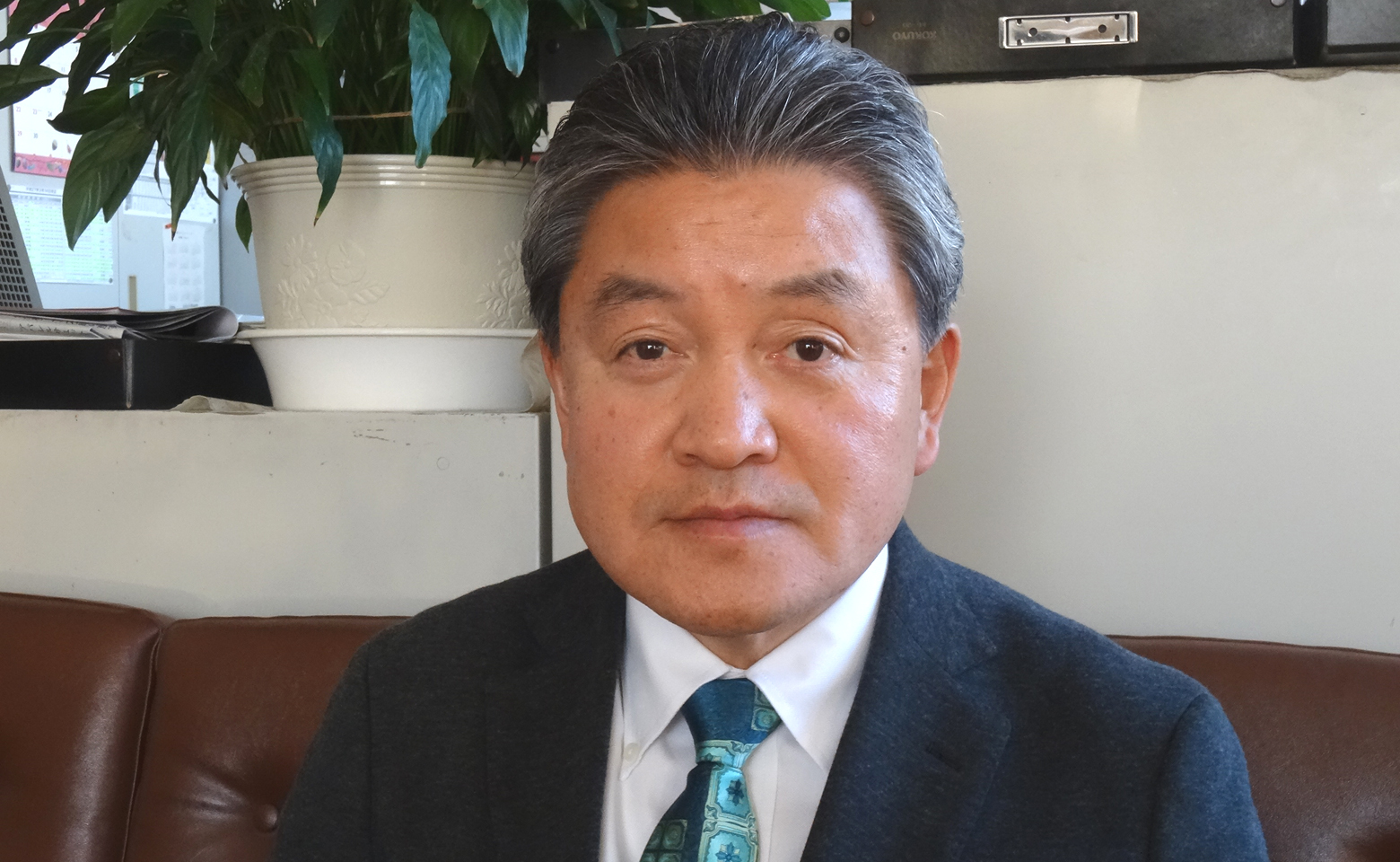
NHKの朝の連続テレビ小説「あまちゃん」のロケ地として話題を集めた岩手県久慈市。同市にある岩手モリヤは、婦人ジャケットやコートを中心に高品質なモノ作りを提供する日本の代表的なアパレル工場として知られています。東日本大震災直後からは電力削減や改善活動を全社的に行って来たそうです。今、日本で差別化商品作りを目指す企業から仕事の依頼が途切れないと言います。今年5月に設立された一般社団法人「北いわてアパレル産業振興会」の代表理事も務める森奥信孝社長に同社の取り組みや国内工場の方向などをお聞きしました。
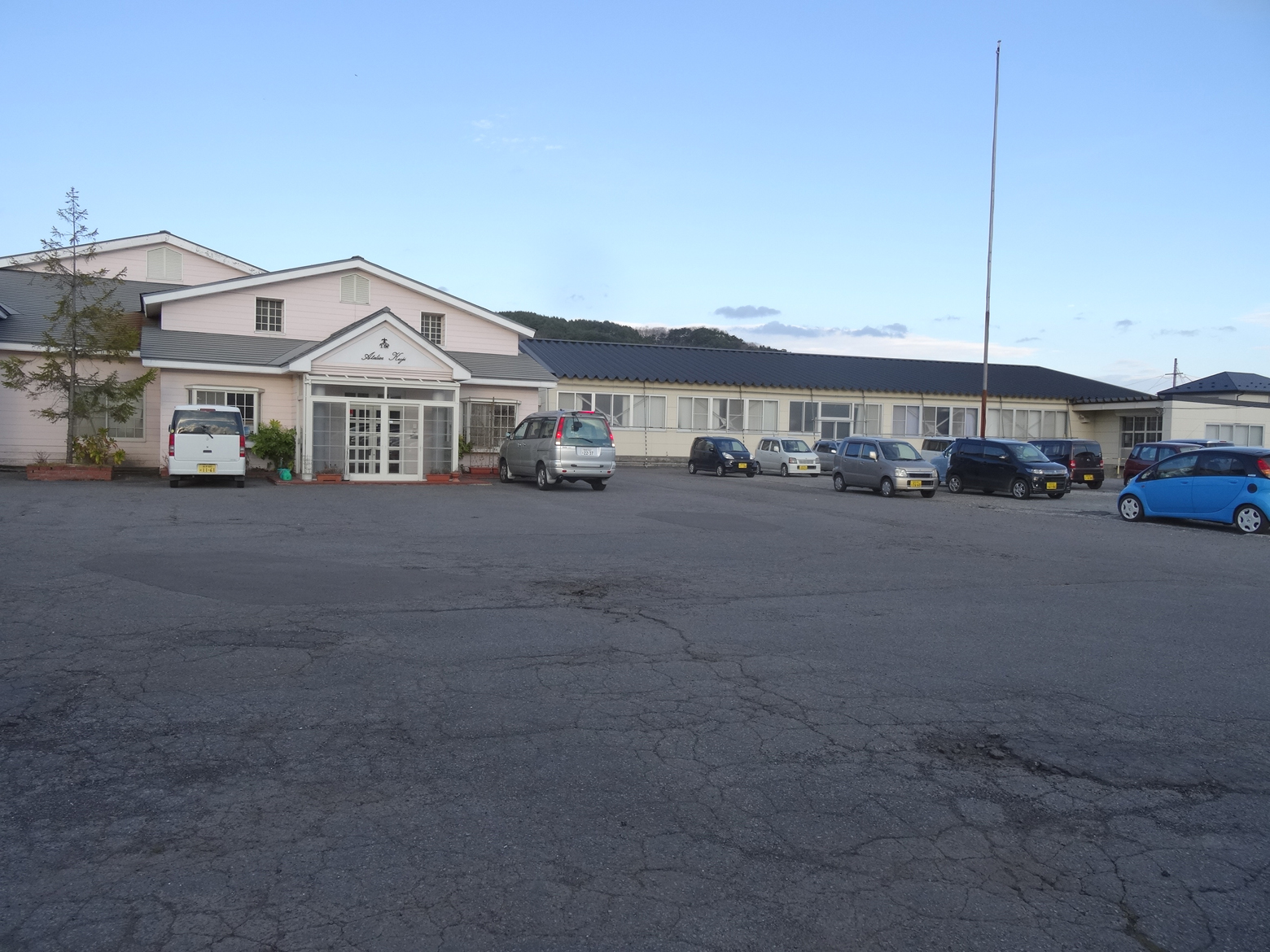
岩手県久慈市にある従業員93人を擁する岩手モリヤ
高い完成度で高級ブランド生産
ー東日本大震災後から電力消費量の削減や改善活動に取り組んできたそうですね。
大震災でこの地域も津波被害は大きく、工場も1週間操業が止まって、ボク自身も避難所生活をしました。節電はその体験がきっかけで、まず社員に使ってない蛍光灯を消すことを呼びかけ、蛍光灯も全部LEDに切り替えた。それだけではあまり節約にならないので、電気容量を多く使う機械を省エネ型に切り替えた。スポンジングマシンは熱源が電気から蒸気の機種に換えたら10分の1以下に。接着機も縫製場のプレスの電気ボイラーも入れ替えた。大型の量産タイプ2台が稼働していたCAMも1台に減らし、新たに1枚裁ちを取り入れた。設備はそういう省エネタイプに変更したが、何といってもここは冬場が長く、半年以上暖房が必要です。その電力対策として吹き出し式の暖房機を止めて、灯油のパネルヒーターを導入し、縫製場の窓には二重サッシを取り付けた。一方で整理整頓の5Sを中心とした改善活動にも取り組んできたんです。棚を増やして生地や小物類、道具などを分類し、見える化をやってきた。そして昨年4月には省エネと改善の両方を兼ねて大改革を行った。当社の工場は裁断棟と2つの縫製棟があって、縫製は1棟に2ラインずつ計4ラインが稼働していた。その縫製場の1棟を機械置き場にし、すべてのラインを1棟に集約した。縫製場の出入り口には寒さ対策のビニールカーテンも取り付けた。型替わりになると使用するミシンも変わってくるので、毎日ミシンは入れ替える必要がありますが、縫製を集約したことで管理者や人、作業中の身頃の移動が少なくなり、逆に効率が高まる効果も現れている。電気料金は1昨年から17%上がりましたが、現在、電気使用量は震災前と比べて40%削減に成功しています。震災を経験したからこそ、こういう大きな改善につながったわけですね。
ー岩手モリヤさんは、高い完成度のモノ作りで高級ブランドを手掛けられています。
縫製業は労働集約産業でどっちかというと技術者に頼る、人に頼るモノ作りです。しかし当社は付加価値の高い製品を手掛けていても人の勘や経験、テクニックに頼らないモノ作りを目指して機械化を進めて来たから今があると思っています。もちろん技術者の育成に取り組んでおり、今年度も技能検定の婦人子供既製服縫製作業の1、2級を8人が受験します。ほかの工場とちょっと違う特徴というのは完全内製化。高級品だからシワを作らない服作りに取り組んできたわけです。シワを作らないために社内の組み立て工程ではハンガーシステムで搬送する。社内でせっかくシワを防いでいるのに、まとめ屋さんに出すと結わかないといけない。それをやりたくないから内製化した。内製化するために手作業を出来るだけ改善し、機械化できる工程は機械化してきたんです。
勘や経験に頼らない服作り
ー社内で生地試験から一貫の仕組みを構築されています。
これも勘や経験などに頼る作業をなくすのが狙いです。それには縫製現場はとにかく作業者が迷わないようにすることで、決められた縫い代で生地の端と端を縫い合わせることが出来るようにするのが基本。そのためには正確な裁断が必要です。当社も以前は粗裁ちし、芯張りしてから重ね直ししてバンドナイフで正確裁断していました。しかし、CAMを導入した時に、せっかくCAMで正確に裁断できるわけだから、一発裁断しようと考えた。CAMで正確に寸法を上げるため、事前に生地の動きを把握する生地試験と生地をリラックスさせるスポンジングマシンを備えた。表素材の生地試験を行い、その情報を基にスポンジングを行い、素材をリラックスさせる。これは素材本来の風合いを大切にすることが良質な服作りの基本と考えているからです。
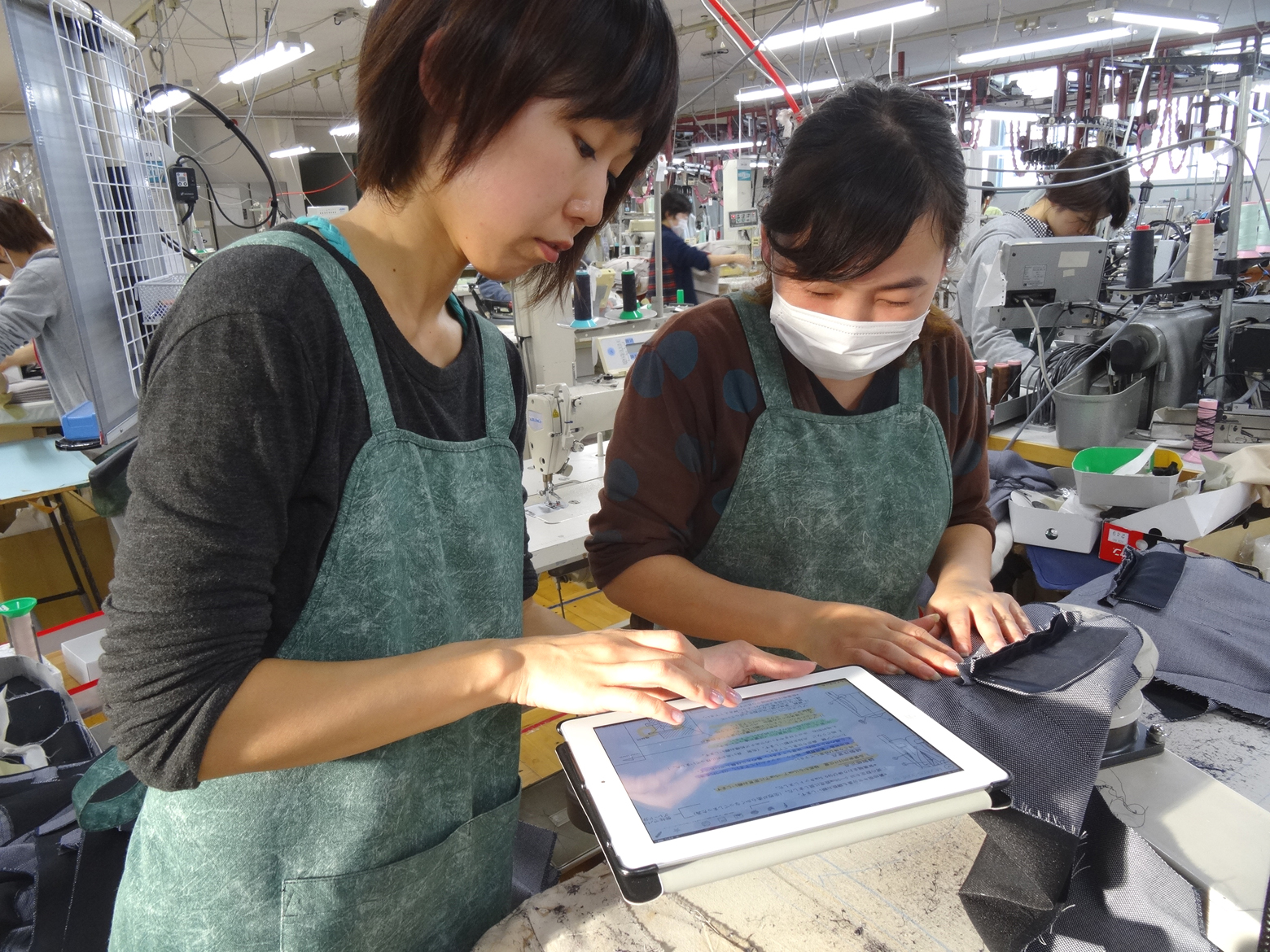
縫製現場での仕様書説明はiPadを活用
震災後、電力使用を40%削減
ーメード・イン・ジャパンへの関心が高まる中、1年ほど前から「閑散期がなくなった」という話をされています。
国内の工場が減少してきたという背景が一つあると思いますが、仕事量は多く、来年3月くらいまでいっぱいです。逆にこなしきれないくらいですね。もう一つの理由として、アパレルさんや小売りの方々も価格競争だけではなく、差別化を図ったモノ作りをしたいという意識が高まっているようです。そのために、より高品質、より高付加価値を求め、我々国内に残っている工場の受注が増えてきている。単にメード・イン・ジャパンで国内生産に戻ってきたということじゃなくて、より差別化を図りたいという要求です。
「内製化」へ機械化が急務
ーそれでも国内工場は減少しています。国内の工場が生き残って行くにはどうしたら良いんでしょうか。
国内の縫製工場はこの12年間で半分になっています。今後もまだ減るでしょうね。そうなると国内で作りたくても作れない時代が来ます。今でも国内は工場不足になって来ているわけですからね。いよいよ個の力ではどうすることも出来ない時代になってきた。やはり川上から川下まで、生地メーカーをはじめアパレル、工場、小売りなどが水平連携していかないと、国内で作れなくなる。最近、国内で生産し海外で販売しているブランドが現れていますが、それはメード・イン・ジャパンがブランド力を支えているわけです。日本の縫製工場で作られた商品だけがメード・イン・ジャパンなんです。今は数を作る時代から、売れるモノを作る時代。製造原価をいかに下げるかではなくて、製造原価を上げても価格以上の価値ある商品を提供するという時代になっています。そのためには製造原価を上げて、国内で生産しても十分に対応できる仕組みを作ることであり、それには目先の労働コスト追求ではなくトータルコストの削減と、プロパー消化率の向上しかありません。業界全体でそれに取り組めば、国内工場は十分生き残っていけます。
「北いわて」の産地振興にも力
ー今年5月にスタートした北いわてアパレル産業振興会の代表理事として産地振興にも力を入れていますね。
振興会は16社が加入し、総従業員数は1,150人にのぼります。久慈、八戸、二戸のエリアは縫製業が集積し、久慈市では縫製業の従業員が全製造業の約2割を占めるほどで、縫製業は北岩手の基幹産業になっています。振興会でも全国に向けて「北いわてはアパレルの聖地だ。」というキャッチフレーズを掲げているんです。縫製業の特色は女子型企業で従業員の約9割が女性であり、地域に根強く浸透し、県もビジネスマッチングフォーラムの開催やJFWジャパンクリエーションへの出展など一生懸命応援してくれています。振興会立ち上げのきっかけは、過去2回開き、来年2月28日に第3回の開催を予定している学生ファッションショー。これまでは県の出先機関である県北広域振興局が主催でしたが、今後も県が主催というわけにいかないので振興会を立ち上げ、そこを支援する形に切り替えて欲しいと依頼された。これからは振興会が主催になります。同時に会員企業は生産性向上、技術力向上、人材育成、改善活動など共通の部分はアイテムを超えて勉強し合っていくことにしており、具体的に工場見学、意見交換会の活動も始まっています。また来年2月のショーでは「北いわてブランド」も打ち出します。7月に岩手県と連携協定を結んだ文化学園の協力を得て、現在9社が作品を製作しています。こういう新しい取り組みで社員のモチベーションアップなどにつなげたいと考えています。
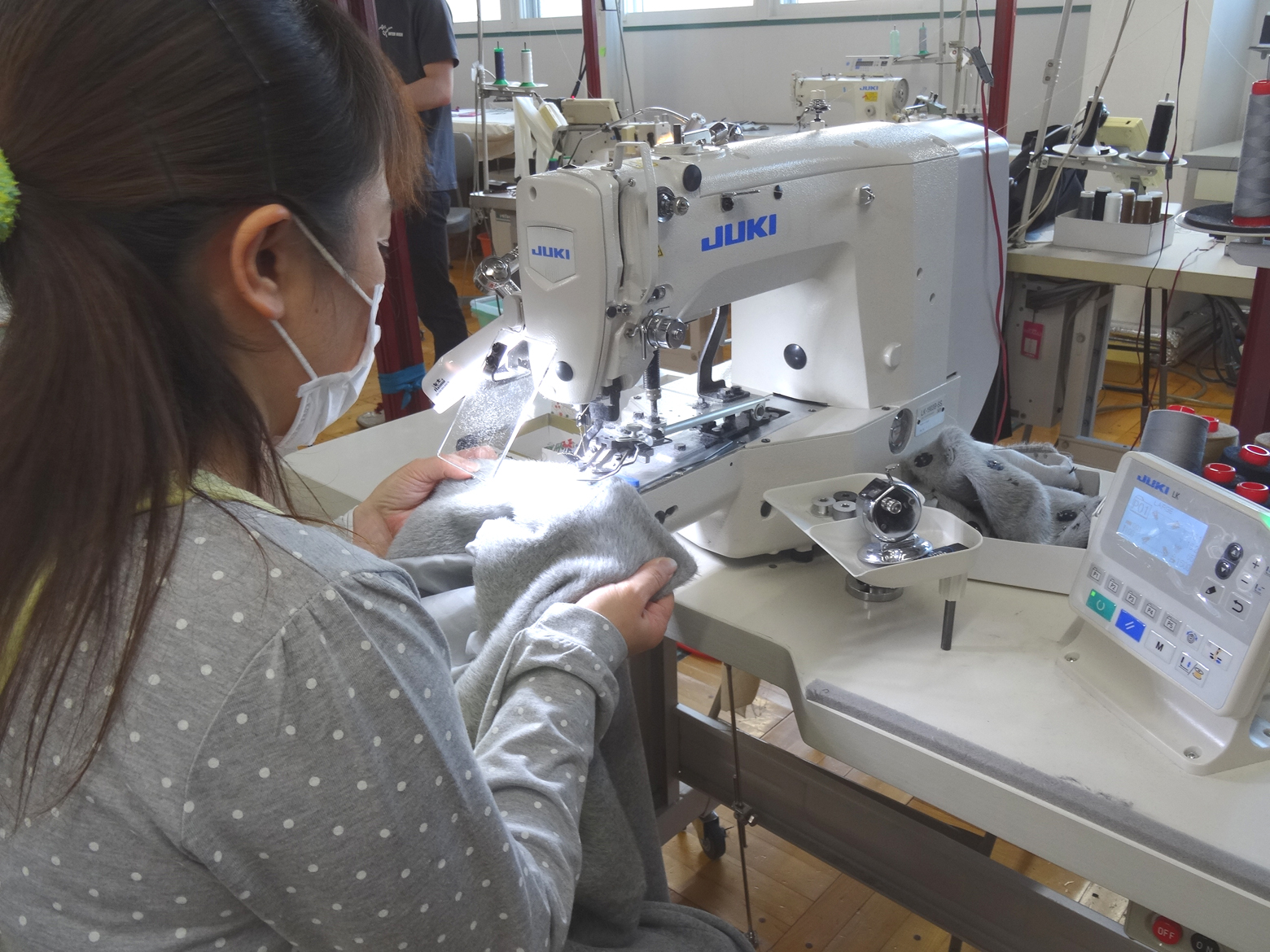
高速電子本縫いボタン付けミシン「LK-1903B」
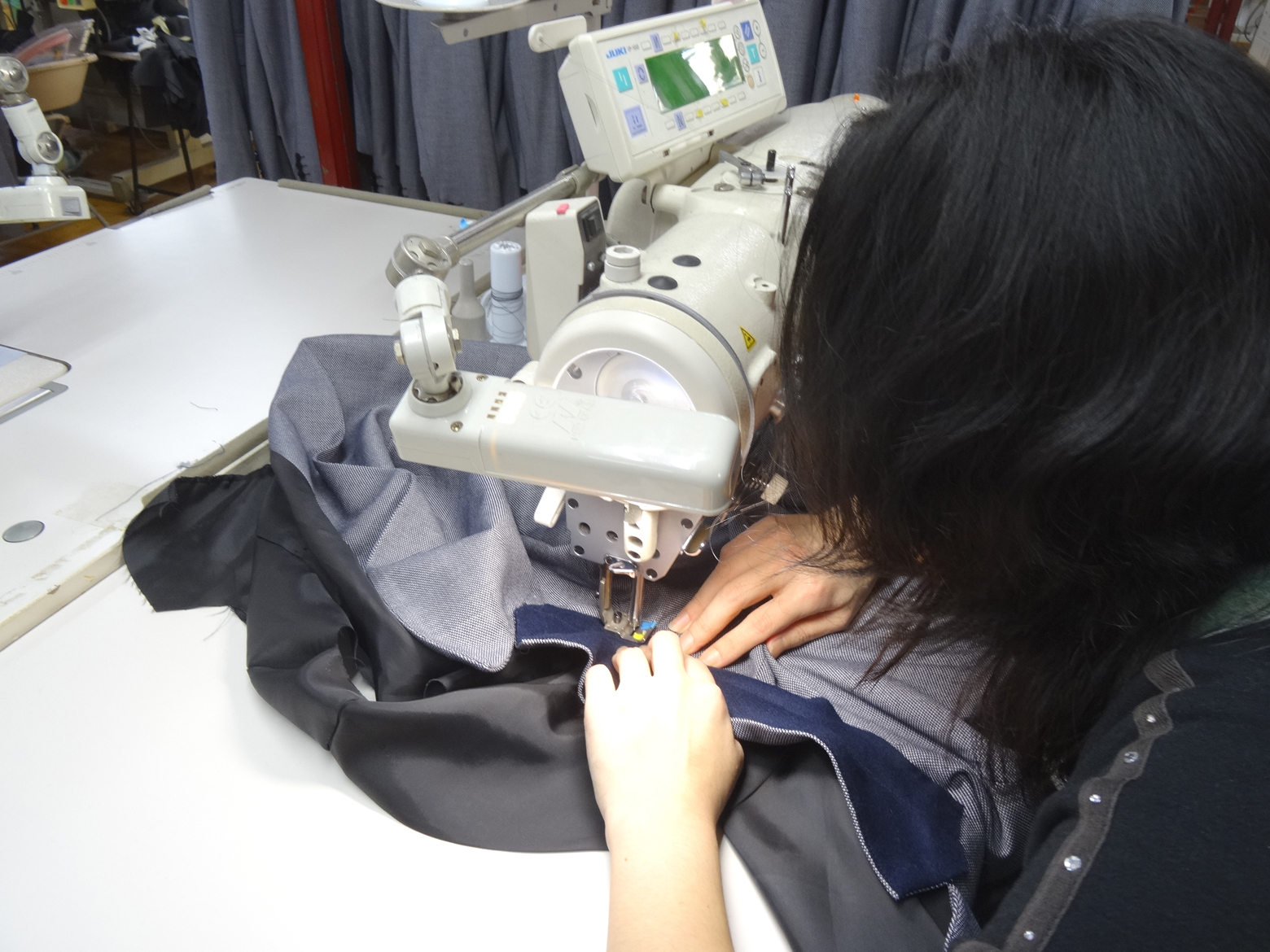
ダイレクトドライブ高速電子本縫い千鳥縫い自動糸切りミシン「LZ-2290A-SR-7」
JUKIは世界のアパレル生産を全力でサポートします
スナップ付けの機械化へ--「AMS-210EN」導入
JUKIの製品では、今年は入力機能付き電子サイクルマシン「AMS-210EN-1306」を導入しました。まとめ関係の機械化が目的で、スナップ付けに活用しています。JUKIは岩手県内にJUKI販売の東北カスタマーズセンターがあり、メーカーのフォロー体制が整っている点で、我々も安心して設備投資が出来ます。
今、国内の縫製工場で技術力があるところが逆になくなっていっているという状況が現れています。ほとんどの縫製工場は人に頼るモノ作りでずっと来ているため、優秀な技術者がいるほど、その人たちに頼ってしまうんです。しかし少子化、人口減少、それから学卒者が集まらないという、過去になかった新たな問題が出ています。つまり人が入ってこない分を設備に置き換えていかないといけないと思うんです。そうじゃないと何も前に進みません。どんどんじり貧になっていくだけです。
当社は、付加価値の高いモノ作りをしている中でも人の勘、経験、テクニックに頼らないということで機械化を進めて来たから今があるんです。高級品を手掛けているだけに完全内製化し、シワを作らない服作りに取り組んできました。しかし、付加価値が高ければ高い商品ほど手作業を求められます。手作業が多くなると、まとめの内製化をしているデメリットとして、手作業に回る人をラインからはずさなければいけなくなります。通常のまとめはパートの人などで対応できても、手作業が増えるとミシンやアイロン工程の人がまとめに入るようになり、生産枚数も落ちるわけです。
だから今、アパレルさんにも言っていることは、出来るだけ手を抜くんじゃなくて、手作業を出来るだけ改善し、機械化できるモノは出来るだけ機械化していきたいと。今まで手でやっていたボタン付けとかスナップツケとかホック付けとかは機械でやっていかないといけないでしょう。ボタン付けやスナップ付けも、手作業が良いかというと、決してそうじゃないんですよ。また針を持てる人もだんだん減ってきて、数年先を考えてみると、そういう工程を機械で置き換えた方が正確な仕上がりが得られるし、品質が安定します。
つまり人の勘、経験、テクニックに頼らないモノ作りするための機械化というのは安定した品質のための機械化です。機械で出来るところを人間がやるんじゃなくて、機械が出来るところは出来るだけ機械にやらせて、その分、もっとより高度な工程を人がやっていく。そういうことでどんどんレベルアップしていくために機械化をするわけです。そういう意味で、今後の縫製工場の取り組みは機械メーカーと切っても切れない関係になると思います。
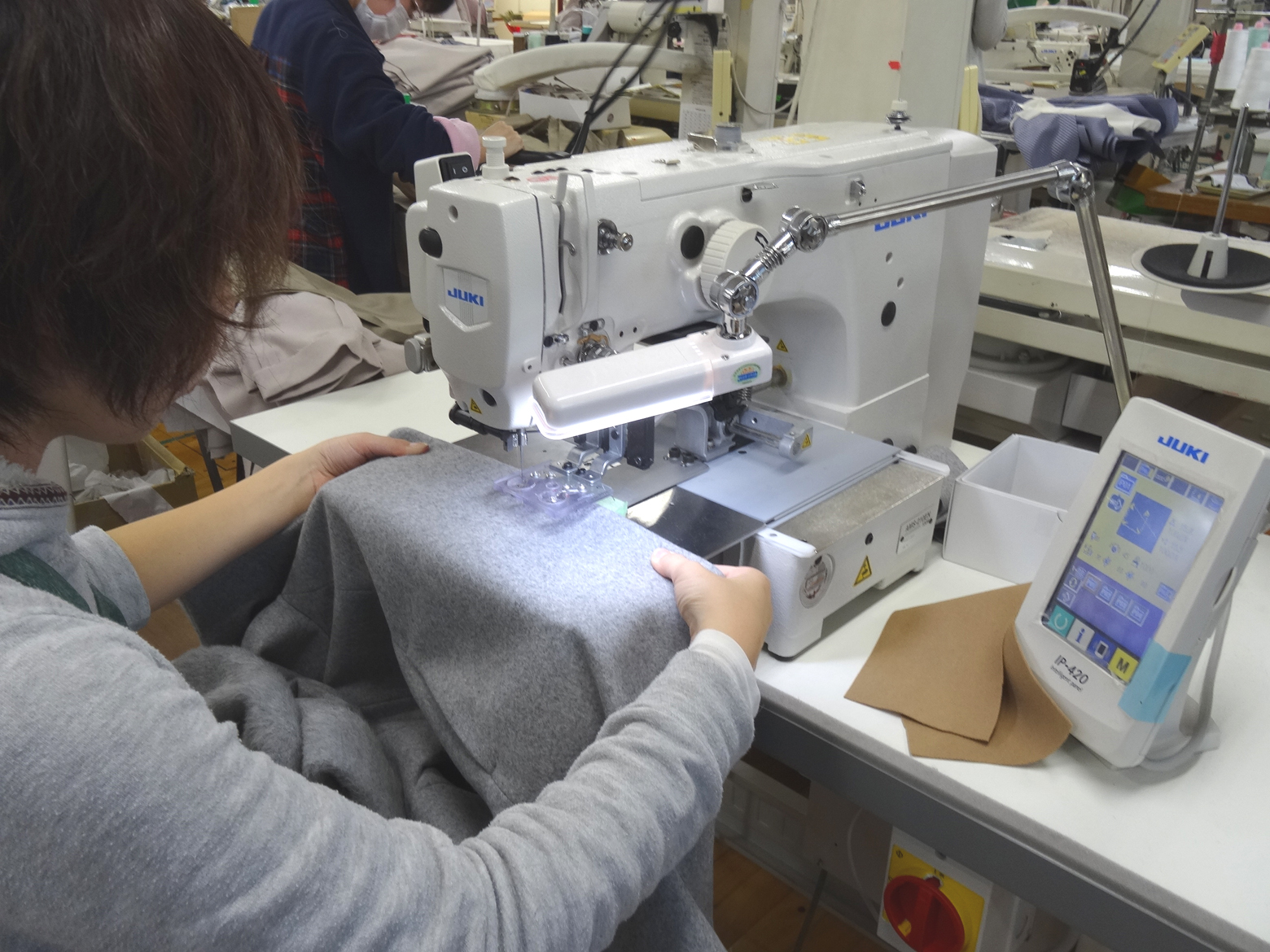
スナップ付けに活躍する電子サイクルマシン「AMS-210EN-1306」
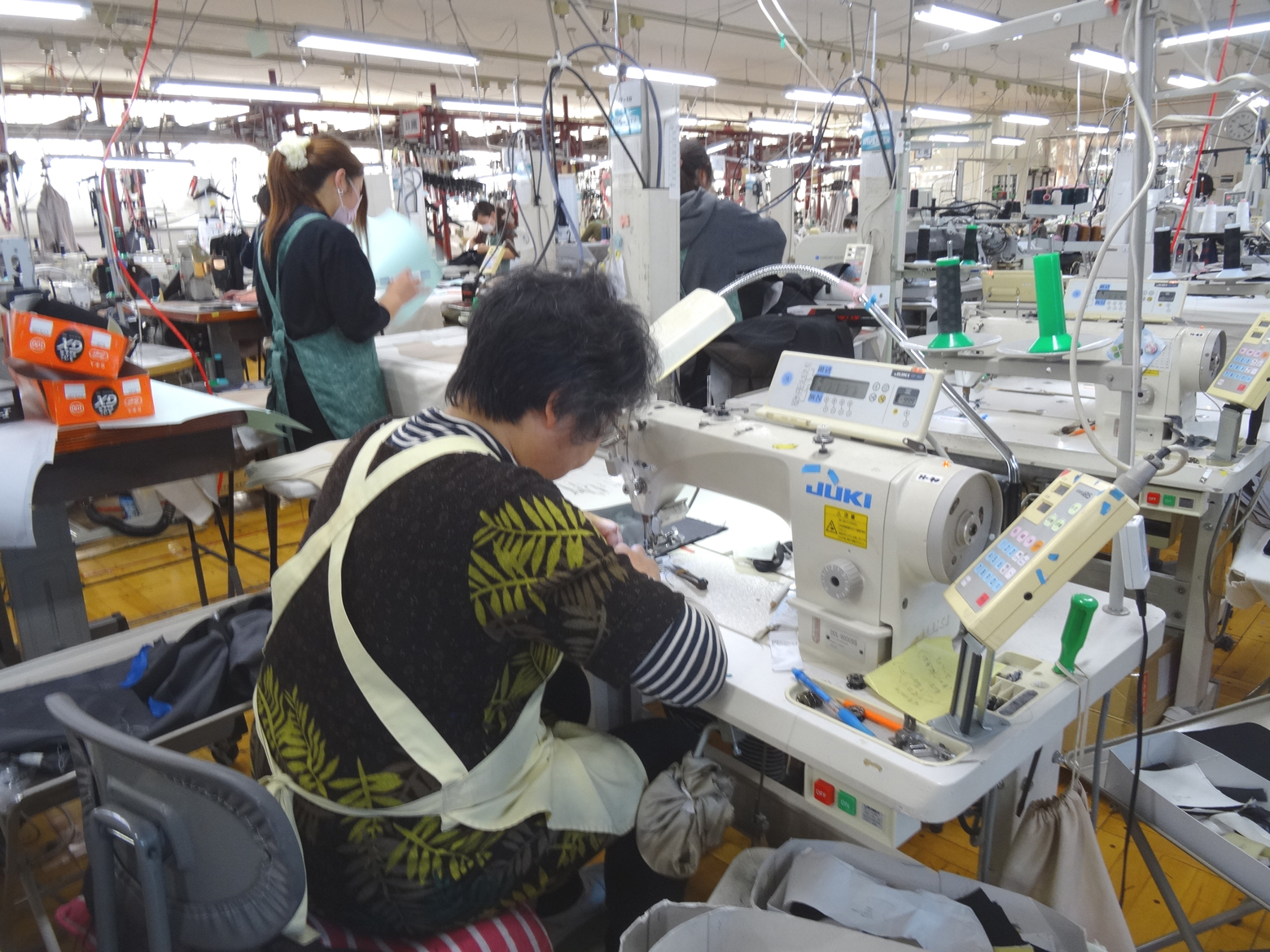
完全内製化しシワを作らないモノ作りを追求