生産現場に『JUKI』を探る Vol.1
第1回・プロローグ
JUKI大田原工場
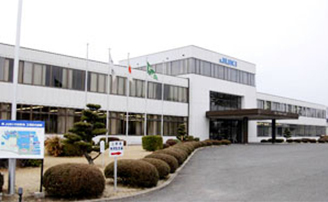
アパレル工業新聞とJUKIは2002年4月からコラボ企画をスタートし、これまで第一次=「服作りコミュニケーション」、第二次=「服作り新時代」を掲載してきた。今号から第三次企画=「生産現場に『JUKI』を探る」を登場させる。
国内生産の生き残りをかけて
日本独自の「優位性」を追求
JUKIの業績好調が続いている。これには、中村和之社長を先頭に進めてきた構造改革が、グローバル市場への的確な対応など様々な要因と結びつきながら、軌道に乗ってきたことがあげられる。そうした中、忘れてならないのが製造部門の構造改革である。
その中核が、栃木県大田原市にあるJUKI大田原工場。工業用ミシンで世界トップのJUKIは、国内のほか中国、ベトナムに生産拠点を持つが、そのマザー工場が大田原工場で、(1)高付加価値製品の生産拠点(2)開発・新製品生産の展開拠点(3)海外生産に対する支援拠点-の役割を持つ。JUKIの高級機種を生産。このほどデビューした本縫いミシンの最高峰モデル「DDL-9000A」シリーズも大田原工場で生産が始まっている。この4月から、別会社の「JUKI大田原株式会社」からJUKI本体に合体したが、大田原カンパニーとして、実体は変わらない。
大田原工場の操業は1971年。ロックミシン(MOシリーズ)の生産工場としてスタートしたが、2年後には本縫いも本社から移管。文字通りJUKIの主力工場になった。その立ち上げから第7次プランまで大田原工場にいて、その後、中国、ベトナムの工場で辣腕を振るい、3年前に再び大田原に戻ってきたのが上席執行役員大田原カンパニー長兼工業用ミシン事業部副事業部長の山岡修二工場長。「海外に10年いましたが、その前の20年は大田原にいたから、隅々まで知っています」と話す山岡氏は、精悍で古武士のような風貌。液晶モニターの端末を自ら操作しながら、工場改革についての説明は延々3時間以上に及んだ。「国内生産の生き残りをかけて、日本の工場に何が出来るかということを常に考えている」と話す山岡氏。例えば、中国は人件費が上がってきたとは言っても「日本は人件費で15倍負けている」。しかも、JUKIの100%子会社だから、苦労して蓄積してきた日本の技術やノウハウの移転を図らなければならない。その上で、日本の工場として存続し、発展していくためには「日本独自の優位性が必要」だ。
「モノ作りの工法と管理がキーポイント。まず自分達の足元を見ること。そして目標を設定する」。2004年度の1月、山岡氏が幹部と社員へ発したメッセージである。2005年から始まる中期計画で、「3年分を2年で達成してしまうぐらいのレベル」で、改善改革が進んできた。しかも、「初心を忘れず、足元をいつも見つめ直し、モノ作りで生き残れるために何をするかというチャレンジを絶えずしている」。
JUKIブランドのマザー工場として、オンリーワンの「優位性」を持ち続けるため大田原工場が掲げているのが「デジタルファクトリー」への挑戦。2004年から変種変量に対応できるモノ作り、高付加価値生産を目指してきたが、「モノ作りの原点は人」。山岡氏が管理監督者に常に言っていることは、「きちんとした思想を持って、集団の組織力として導くこと」。
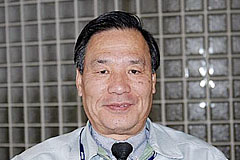
山岡修二工場長
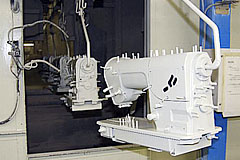
DDL-9000A
変種変量にデジタルセル生産で
管理監督者と優秀なモノ作り技能者。モノ作りに携わっている人が362人。そのうち69%が国家検定認定の技能集団。しかし、それだけでは国内で優位性は発揮できない。「技能にさらに磨きをかけるのは必要だが、道具としてのプラスワンがデジタル=IT技術。単純な言い方をすると、IT技術と磨かれた基本技能によるモノ作り」。「しっかりと目的を持った技能を保有しているのは日本人の最大の強さ。今までの技能と最新IT技術を融合すれば、高い技術レベルの維持向上が可能」と言う。
その具体的な挑戦が変種変量生産に対応出来るためのデジタルセル生産。高品質の製品を短納期で作り、変種変量に効率よく対応できることがねらいだ。習熟した技能者のノウハウを次世代に効率よく伝え、未経験者でも早く習熟できる方法としてもデジタルは予想以上の効果を出している。画面に必要とする工具、部品などが全部指示される。しかし、基本技能を持っていることがベースとして必要。例えば、ねじ締め作業。従来の作業標準書をデジタル管理し細かく分解。詳細に作業者に伝達することが出来る。今まで習熟するのに12週かかったのが、デジタルを置いて同じものをやらせると2週で習熟した。習熟だけでなく改善にも大変な武器になった。
セル生産は、無理をしない姿勢の中で作業が出来、人にやさしい生産ラインだ。LK1900Aは、15人のうち10人は派遣社員、つまり未熟練者だが、1年半ノークレーム。「デジタルを用いた無駄取りで、相当レベルの高い生産性の向上が出来る。このデジタルの組み立ては変化しており、まだINGの段階だが、非常に効果があることがわかった」と山岡氏。デジタル技術での基本技能のマニュアル化、基本技能の社内検定。未然防止のための新しい作業標準作成要領の作成。源流対応による本社の商品企画・開発との一体化。「量の世界から質の世界に変わる。今のうちから、日本の得意なIT技術、デジタル化を含めた基本技能を磨けば非常に強いモノ作りができる」。国内でメード・イン・ジャパンのモノ作りを目指すアパレル製造業へのエールとも取れる。
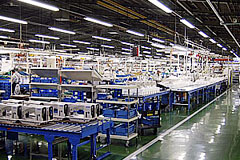
デジタルセル生産
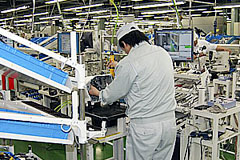
デジタルセル生産
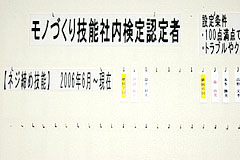
基本技能の社内検定