次世代のモノ作りに挑戦 第30回
株式会社メンズアキタソーイング 代表取締役社長 髙橋 康一郎 氏
メンズアウターで「三ツ星工場」に認定
工程分析徹底し、高い対応力が強み
秋田県仙北市にあるメンズアキタソーイングはこのほど、IACDE(国際衣服デザイナー・エグゼクティブ協会)日本支部から「三ツ星工場」に認定されました。メンズのカジュアルジャケット、コート、ブルゾンをメインにしながらレディスのワンピース、ブラウス、スカートまで、高い品質で幅広いアイテム、仕様、素材への対応力が評価されたそうです。そのベースは服一着を作るための工程表を必ず作成し、複雑な仕様を分かりやすくしてモノ作りを行っていることにあります。こうした同社の生産現場をJUKIのダイレクトドライブ高速本縫い自動糸切りソーイングシステム「DDL‐9000C」を中心とした縫製機器がサポートしています。
―IACDE日本支部から「三ツ星工場」として認定されました
IACDEに入会して8年くらいです。うちはメンズカジュアルがメインで、しかも他がやらないような仕事をやっています。それでも服作りの基本であるメンズのテーラードを学ばなきゃいけないと考えていた時、サンラインの佐藤(克豊)社長が誘ってくれたのがきっかけでした。正統派スーツの企業の方やモデリストのみなさんばかりで、ちょっと異色でしたが。そんな中、今回メンズアウター分野として三ツ星工場に選んで頂きました。7月12日に東京で開催されたIACDE日本支部設立45周年記念セミナー&パーティーの場でサンラインさんと当社の2社が認定証を受賞し、席上、柴山(登光)先生から『デザイナーズブランドのような凝ったデザイン、他がやれない素材、仕様をこなす対応力に優れている』と講評して頂きました。
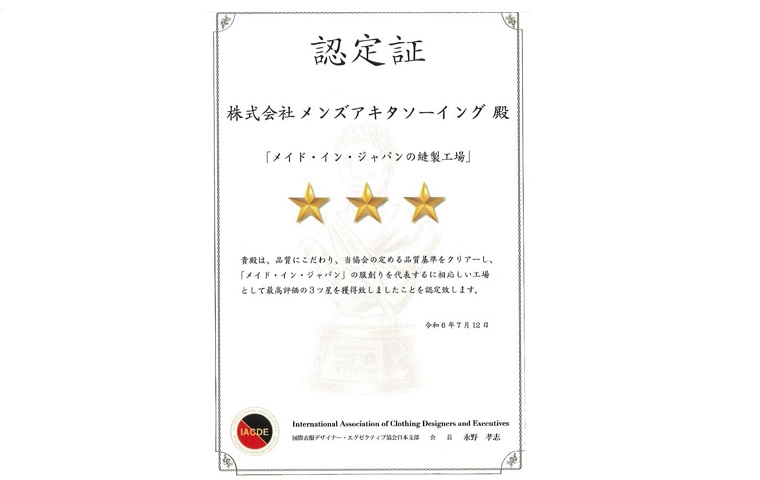
「三ツ星工場」の認定証
―現状は
現在、グループ全体で約80人です。外国人実習生も中国人が4人、インドネシア人が3人おり、来年3月末には中国人全員が帰国し、新たにミャンマーから受け入れを計画しています。地方にある工場ですから外国人を受け入れないとやっていけませんが、やる気のある若い日本人が入ってきたら積極的に教育して技術者に育てようと思っています。
―社内の構成は
管理者やサンプル担当を含めると縫製部門が約50人で、間接部門の比率が高いのが実情です。と言うのは、縫製上がりのまとめや仕上げプレスはすべて社内一貫体制。しかも縫製だけの100%外注工場が2つあり、その裁断から仕上げプレス、まつり、検査もこちらでやっています。だからCADも東京の営業拠点分を入れると約10台あり、うちくらいの規模でもCAMを3台導入し、CADと裁断で約10人、仕上げプレス、まとめ、検査に約25人が携わっています。社内の縫製ラインは20人と25人の2ラインで、あれは縫えない、これは縫えるとなるので両方とも同じようなものが縫える形にしています。サンプルは2、3人が担当していますが、一人丸縫いができる技術者が5、6人いますので、いつでも応援に入れます。
―生産アイテムが幅広いですね
メインがメンズのカジュアルジャケット、コート、ブルゾンで、レディスのワンピース、ブラウス、スカートもやりますし、カジュアルパンツも手掛けます。今はメンズが6割で、新しい仕事のお話があるのはメンズが多い。当社は紳士コート工場としてスタートしたので社名にメンズを付けていますが、その後、レディスや子供服もやり、僕が会社を引き継いだ時はレディスが8割で、取引先も大手百貨店アパレルが中心でした。しかしレディスのマーケットは競合が激しく、当時2割だったメンズのカジュアルを広げ、開拓していこうと考えたんです。メンズカジュアルはファスナー付きのポケットがたくさんあったり、ライナーがくっついたり面倒な仕様が結構ある。そういったものを受けていたら比率が高くなった。だから時代のニーズが変わるとともに様々な挑戦を続けてきたわけで、これしかできませんという工場ではなかった。だから生き残ってきたんです。
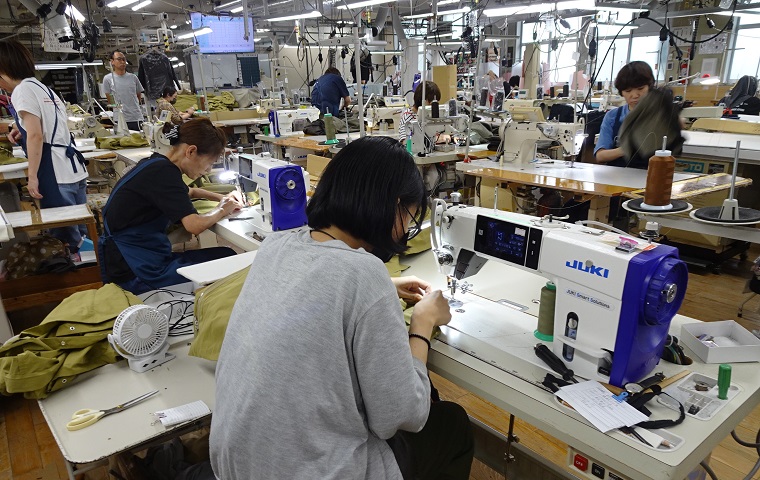
幅広いアイテム、仕様、素材に対応できるのが強み
―そういう多様な仕事をこなすために工程分析を徹底しています
工程分析は、基本的に工程に対して必ず秒数を測り、オペレーター一人ずつの能力も数値化しているので、その秒数の一人ひとりへの割り振り、要は生産管理のツールですが、それだけではなくて、難しい仕様を見える化して簡単にするというのが一番の目的です。工程を書き連ねて見える化し、その工程分析があれば誰でも工程が組めるという形にすることによって大変な仕事でも量産として流せる工場にしています。これは亡くなった父である先代がどうしたら服作りをシンプルにできるかと考え、JUKIさんが提唱していた工程分析の手法を取り入れ、独自に確立したものです。父から引き継いだ私は、せっかくいいツールがあるんだから、それを生かして今までやったことがないもの、付加価値が高いものに挑戦した。だからフルアイテムに対応できるし、複雑な仕様のデザイナーズブランドにチャレンジすることもできています。
―具体的にどう進めていますか
サンプル担当が作成時に工程を書き出し、ストップウオッチで秒数を取り、事務所で工程分析表を作成します。それに基づき縫製ラインのリーダーが個人個人に工程を割り振ります。個人のデータは3カ月に1回くらい見直します。ミシンやアイロンなどの設備もリーダーがレイアウト表で示し、それに基づいて男性社員が設備を組み替えます。この工程分析はロットに関係なく全品番必ずやります。多いと2、3万秒、少ないと4千秒くらいの品番があり、本当に様々です。工程分析をやることによってコスト計算ができるし、なにより複雑な仕様が分かりやすくなり、バランス良い量産ができます。また取引先に対して正確な納期を伝えることが可能です。
フルデジタルを10台以上
―縫製現場ではJUKIのデジタルミシン「DDL‐9000C」も多く採用されています
この数年、本縫いミシンはフルデジタルの9000CFに切り替え、すでに10台以上採用しています。縫製現場で使っている人たちは操作が軽いので取り合いになるほどです。うちはコートとかいろんなものが流れるので、広くしたり狭くしたりできるようなテーブルをオプションで提供してもらいたいし、それとデジタルミシンは押さえ圧と送り歯の調整がタッチパネルでできるので楽になりましたが、いずれドライバーが必要のないミシンも開発して欲しいですね。
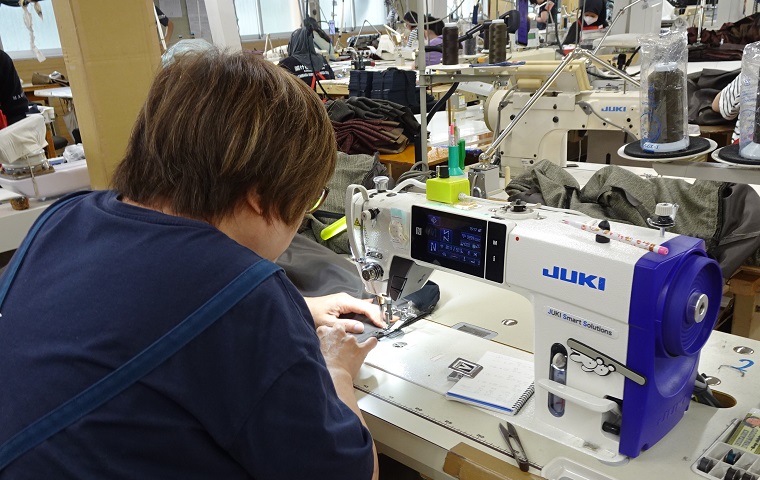
軽くて使いやすいと社内で好評なフルデジタルソーイングシステム「DDL-9000CF」