次世代のモノ作りに挑戦 第22回
ミドリ久慈衣料株式会社 取締役社長 川代 利幸 氏
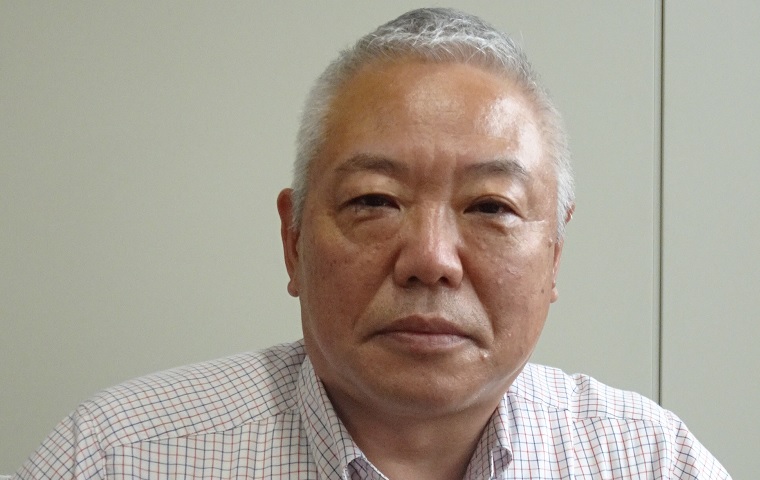
ミドリ安全グループのユニフォーム工場
トヨタ生産方式で多品種少量に対応
安全保護具メーカーのリーディングカンパニーであるミドリ安全グループ。岩手県久慈市でユニフォームを生産しているミドリ久慈衣料は、同グループの国内にある自社工場の1社です。1985年4月の設立当初からトヨタ生産方式「TSS」を導入、ジャスト・イン・タイムの思想に基づく多品種・小ロット・短納期生産を確立し、シャツ、ブルゾン、つなぎ、食品白衣や半導体などの無塵衣向けフードをはじめ様々な業界のユニフォームを手掛けています。改善提案制度やQCサークル、自主研のTPS活動を通じて人材を育成し、工場内ではあらゆる所に改善や工夫が見られるのが特徴ですが、JUKIの「DDL‐9000C」シリーズをはじめデジタルソーイングシステムも多数取り入れています。
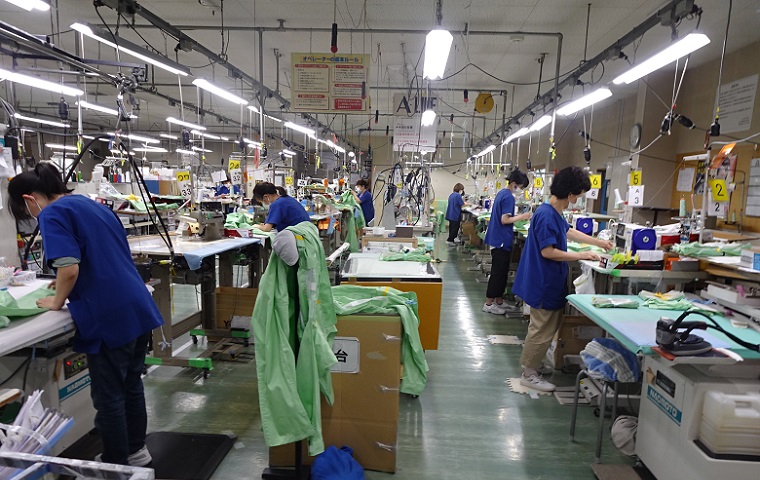
Uの字・立ち作業・多工程持ちでフードやウエアなど多品種を生産
ーミドリ安全グループでユニフォームを生産しています。
ミドリ安全グループのユニフォーム生産は、埼玉県草加市にあるエムシーアパレルが企画・デザイン、研究・開発、生産管理を行っています。国内の生産拠点は我々のミドリ久慈衣料と、福島県石川郡浅川町にミドリ浅川衣料があり、ミドリ久慈衣料の子会社としてズボンを縫製しているミドリアパレル中央 (岩手県岩手郡葛巻町)の3工場です。海外はベトナムのハノイ近郊に800人の第1工場、1千100~200人の第2工場があります。久慈衣料が無塵衣、浅川衣料が防寒服を手掛けているのが違いで、国内工場は売れているものを素早く提供する狙いから両工場ともブルゾンやシャツなどだいたい同じアイテムを生産しています。久慈衣料は現在72人で、今年の新卒者採用はゼロでしたが、毎年1、2人を採用してきた。またベトナム工場から8人を実習生として受け入れている。ベトナム工場でも数ラインでTSSを導入していますので、日本の考え方、改善活動などを学んでもらうため研修をしています。
ーユニフォームは海外生産が主流の中、国内にもしっかり拠点を持たれています。
ミドリ安全グループはカタログ商品とお客様の特注品、つまり各社のオリジナルユニフォームを提供しています。オリジナルユニフォームの比率が高いので、お客様へのサービスやサポートをするには国内に工場があって、小回りが利く体制が必要になります。定寸に当てはまらない人向けという細かい生産を海外ではやりたがりません。ミドリ安全グループは国内の自社工場を持ち、そこをしっかりとコントロールしフォローしていけるのが強みです。毎月5点、10点といったオーダーも少なくありませんが、それに対応できるのは日本国内しかないんですね。その代わり様々なオーダーが来ます。例えばカーテンもありましたし、帯電防止のボンベカバー、半導体工場で使うカバンとか。本当に多品種小ロットの生産です。
ーそれに対応しているのもジャスト・イン・タイムの生産システムがあるからですね。
グループで1番最初にTSSを導入した工場で、1985年の工場設立時から1年間、アイシン精機にトヨタ生産方式を指導して頂きました。グループのプロジェクトとして、グループ各社から1、2人来て、一緒に勉強しながら立ち上げ、その人たちが各社に戻ってトヨタ生産方式を展開していったわけです。生産現場はA~Dの4ライン編成で、Uの字ラインの立ち作業、多工程持ち、1枚流しです。受注時に「カンバン」になる指図書を作成し、それがCADや裁断、準備、組み立てラインに順番に流れて行く。各ラインでは工程長(班長)がレイアウト図を作り、生産管理担当者がミシンやミシン糸、アタッチメントなどを準備し、品種替えの時に外段取りをします。かつては工数が少なかったので1人3工程持ち程度でスムーズに動いていましたが、最近は工数が多くなり結構大変。1人5、6工程持ちになり、指導に時間が掛かったり、忘れたり、実習生がなかなか覚えられなかったりと。現場では工程を入れ替えたり、1人ができる工程を増やすため多能工訓練を続けています。
ー工場内では改善や工夫の様子が随所に見られます。
トヨタ生産方式は改善がキーワードで、改善提案制度、QCサークル、TPS活動を継続してきました。 改善提案活動は全員が参加し、1人ずつが手掛けた改善と効果を報告し、毎月最優秀賞、優秀賞、事務局賞を表彰し賞金を渡します。毎月1人2点で130点以上集まります。ベトナム人実習生は難しい面がありますが、日本人社員は全員出してくれます。QCサークルは1年に1度、5~8月の約4カ月間掛けて各部署で1テーマを終わらせます。最優秀賞グループはミドリ安全グループの発表会に参加します。TPS活動はトップダウンの改善活動で、合同自主研と社内自主研がある。合同自主研はミドリ安全グループ各社からメンバーを集め、対象会社に出掛け約10日間で改善活動。持ち回りで我々も3年に2回くらい受け入れます。社内自主研は年2回3日間で、例えば「Aラインの生産性を10%アップ」という私の指示のもとに各ラインから選んだメンバーがAラインで改善活動をします。ベトナム人実習生もQCサークルや自主研に参加して勉強しています。
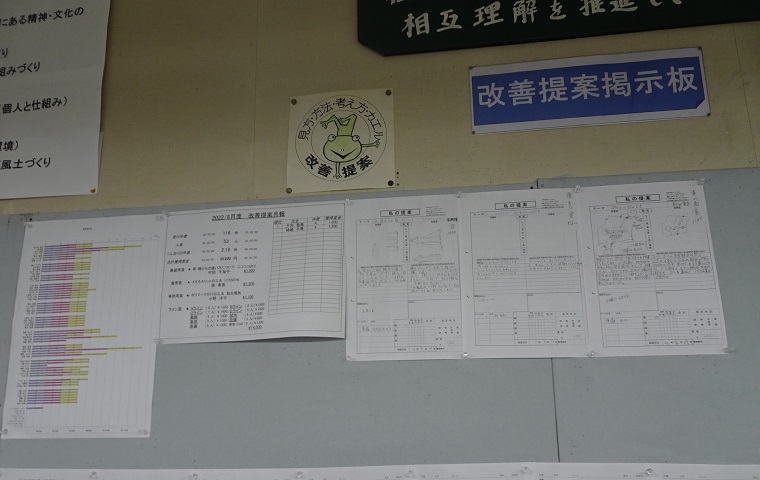
毎月1人2点の改善を手掛ける改善提案制度などで生産性や品質の向上へ
デジタルミシンを57台導入
ーJUKIのデジタルミシンを多数導入されています。
DDL‐9000Cが発売された翌年の2017年に一挙に48台、また昨年2本針や穴かがりの特殊ミシンを含めて9台追加し全部で57台入れています。デジタルミシンは送り歯高さや送りピッチ、押さえ圧などのミシン調整値をデータ化し、タブレットをミシンに近づけるだけでデータが転送できる機能を持ち、段取り替えのミシン調整に最適と考えたわけですが、ミシンに個体差があってなかなか思うように進みませんでした。しかし、ミドリアパレル中央でもデジタルミシンに切り替え、浅川衣料でも新たに約60台を導入しますし、ベトナム工場でも9000Cをかなりの台数採用しています。これだけのデジタルミシンを使いこなせれば、ミシン調整が迅速に可能となり大幅な生産性向上が望めます。日本でサンプルを縫ったミシン調整データをベトナムに送ることもできます。そのためミドリ安全グループ全体で取り組んでいくことになり、エムシーアパレルの生産技術縫技室がデジタルミシン活用の研究をスタートしましたので期待をしています。
「DDL‐9000CF」をはじめデジタルソーイングシステムを57台導入
この導入事例に出てきた製品・サービス
DDL-9000CFシリーズ [プレミアムデジタル]
ダイレクトドライブ高速本縫自動糸切りソーイングシステム
<p>「縫い」の創造。<br />
「縫い」へのこだわりは、次世代ソーイングシステムで変わります。<br />
これまで勘や経験に頼ってきたミシンの調整をデジタル化。<br />
素材に最適な縫いをいつでも再現できるのが、デジタルソーイングシステム、DDL-9000Cです。</p>
詳細を見る
DDL-9000CSシリーズ [デジタル]
ダイレクトドライブ高速本縫自動糸切りソーイングシステム
<p>「縫い」の創造。<br />
「縫い」へのこだわりは、次世代ソーイングシステムで変わります。<br />
これまで勘や経験に頼ってきたミシンの調整をデジタル化。<br />
素材に最適な縫いをいつでも再現できるのが、デジタルソーイングシステム、DDL-9000Cです。</p>
詳細を見る