コアテクノロジー
JUKIのコア技術は、品質を安定させる、使いやすさを追求する、作業性を向上させる、消費電力を削減するなど、製品に直結した技術の数々です。
多様化・高度化する市場ニーズを的確にとらえ、世界中のお客様のご要望にお応えする魅力あふれる機能を生み出しています。
コア技術のご紹介
天秤独立駆動
天秤機構を独立したモータで駆動する技術
縫製中の天秤負荷を検知し、1針ごとの縫い調子を監視する技術です。目飛びや単糸掛けなどが発生したときの天秤負荷を可視化し、良否判定をサポートします。またトレーサビリティ機能としてデータを保存することもできます。
中押え機構との協働によって、縫い始めの目飛びや“鳥の巣”の軽減にも役立ちます。
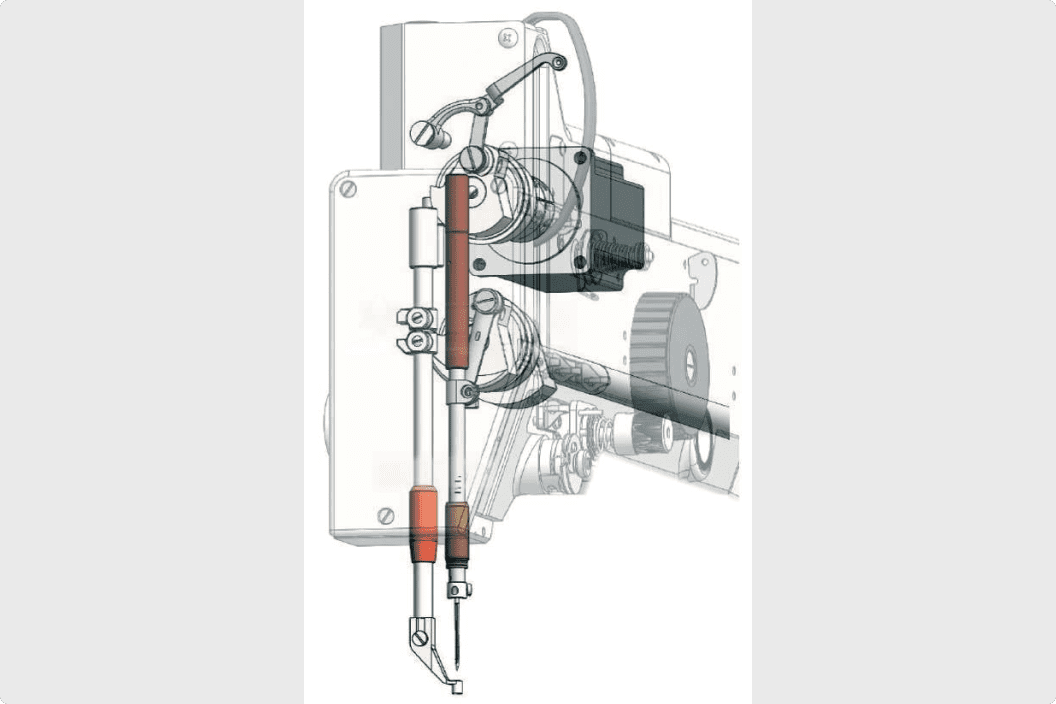
中押え独立駆動
中押え機構を独立したモータで駆動する技術
縫い調子に直接影響する中押えを自由なモーションで作れるようにした技術です。よりきれいで安定した縫い目に調整が可能になります。
生地を押える時間とタイミングがデジタルで調整可能で、生地の浮き上がり抑制や針落ちの安定性向上、目飛び低減に効果があります。
モードを切り替えるとモータ負荷のフィードバックから布の厚みを検出できます。

下糸自動供給
本縫いミシンの下糸を半無限に供給する技術
残糸を除去し、ボビン(下糸を巻き付ける部品)交換を自動で行う技術です。縫製中に釜部、搬送アーム、ボビンセット、残糸除去、糸ほぐし、糸巻き、ノズル、繰り出しの8ステップを一定の間隔で行うことにより、頻繁に発生する下糸交換をなくし、生産を維持できます。

画像処理技術
プログラムデータとのズレ量を画像処理にて補正
パーフォレーション生地など、柔らかく、伸び縮みする素材に対して、生地の縮み量をカメラで測定し、補正しながら縫製する技術です。生地上の目印となる部分から測定し、プログラムデータとのズレ量を算出・補正し、縫い目を確実に目標とする場所に形成できるため、デザイン性を損なわない縫製ができます。

パーフェクトステッチ
1本針CNCミシンの上下独立駆動および同期制御技術
XYの縫製移動方向に関わらずパーフェクトステッチ縫いを行う技術です。ミシンの針上下と釜を独立して回転させる独立駆動と、針上下とXYを同期させて縫製することでヒッチステッチをなくし、縫い締まりや縫い形状を均一化して美しい縫い目を実現します。

デジタル制御
縫い目調整のデジタル化とIoTを活用したデータ転送
送り歯高さ、送りピッチと軌跡、押え圧、上糸のテンションの5つの“縫い目”の調整機能をデジタル化し、数値で記憶できるようにした技術です。調整後のデータは専用アプリを入れたタブレットに記憶させることができ、近距離無線通信NFC機能により、パネルにかざすだけで別のミシンへのデータ転送を可能にしました。

省エネルギー技術
各種モーターをコントロール・最適化し消費電力を抑制
さまざまなモーターの特徴を生かし、ムダなく最大限のパフォーマンスを発揮するJUKI独自のチューニング技術により、消費電力を最適化する技術です。停止時に電源回路をシャットダウンし、稼動時にはすばやく再稼動させる回路設計など、多くの省エネ技術が集められています。

ドライ技術
潤滑油を最大限微量化
高速回転する工業用ミシンに必要不可欠な潤滑油を最大限微量化・低減し、面部をドライ化した技術です。ミシン稼動に最適な状態を探求したJUKIのオリジナル機構で、針棒には超硬質で部品を傷つけない独自のDLCコーティングを施し、半固体の油「JUKIグリス」を少量使用して磨耗を防ぎます。
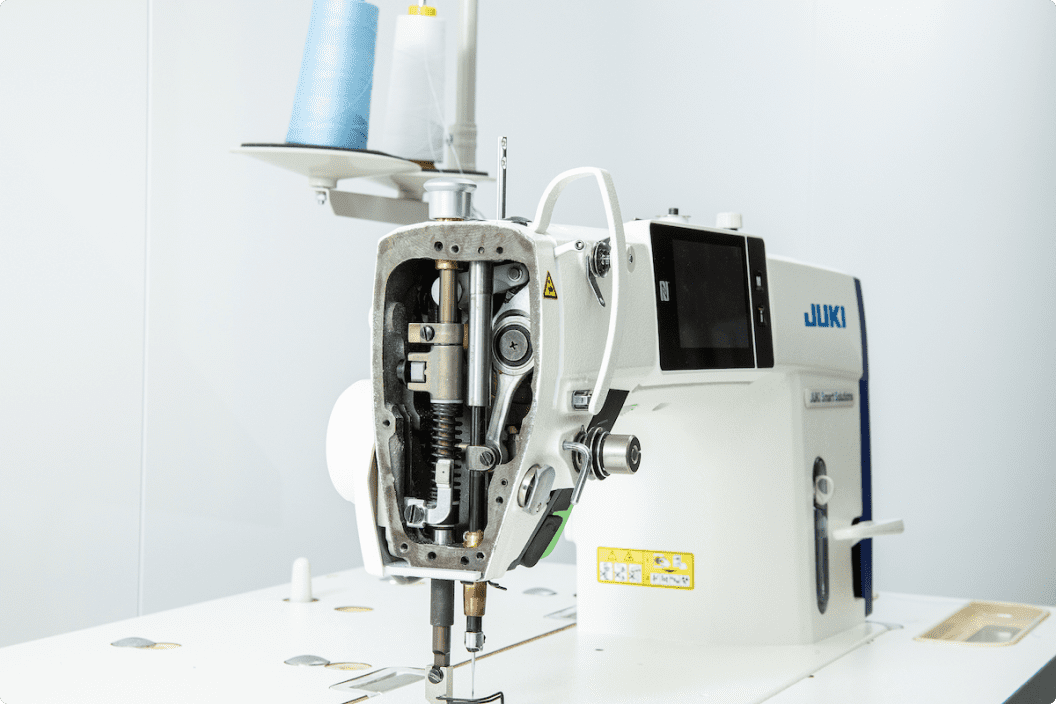
鳥の巣防止・残短技術
糸摘み作業をなくし生地裏の縫い品質を向上
縫い始めに糸が鳥の巣状態になるのを防止し、縫い終わりの糸を極限まで短く切断する技術です。縫い始めに上糸を糸掴み装置で捕捉し、これを縫い終わりまでキープします。縫製完了後、通常の糸切り動作の後、残短用のメス機構で縫い終わりの上下糸、縫い始めの上糸を短く切断し、残糸は吸引します。

アクティブテンション
安定した「縫い」を実現するため、糸の張力を動的に制御
上糸と下糸の張力を絶えず最適化し、美しく安定した縫いを実現する技術です。特殊なソレノイドを電流で微細にコントロールすることで糸調子皿を開閉させ、最良の糸調子を生み出します。厚地・薄地・伸縮などの素材変化による制御、縫いトラブルの防止、模様縫いの制御など、多方面で活用しています。

UI/UX技術
親しみのある操作、分かりやすく使いやすいパネルを実現
スマートフォンと同じ「静電容量方式」のタッチパネルを採用し、画面のタップ、スワイプで直感的に操作ができます。
ユーザーがよく使う機能をまとめて配置し、わかりやすい表示で目的の縫い・操作にすばやくたどりつくことができます。

JUKI Sewing Net
本体に無線LANを搭載し、インターネットを閲覧できる技術
インターネットを介して、ミシン本体内のソフトウェアのアップデートや、タッチパネル画面上で視覚と音声によるガイダンス(YouTube、Instagramなど)の視聴、取扱説明書のWeb閲覧ができる技術です。

ボタンホーラー
職業用ミシンでのボタンホール縫製技術
直線縫い専用の職業用ミシンでボタンホール模様を縫製する技術です。コンピューター制御のXY駆動式の採用により、これまでのメカ式ボタンホーラーではできなかった多種のボタンホールを好みの向き、ボリュームで、送り詰まりのない縫製を可能にしています。

完全自動糸掛け(イージースレッダー)
ロックミシンのルーパー糸通しを風の力ですばやく穴まで通す技術
通し穴に1㎝ほど差し込んだ糸が細いパイプの中を通り、ルーパー穴まで送られる技術です。電動モーターの力でポンプから送られた空気が深さ約0.3㎜の細いスリットを通り、急激に広がることで吸引力を生み、糸を送り出します。糸の摩擦抵抗解消のため、パイプに特殊加工を施しています。

自動糸調子技術
環縫いミシンの糸調子を自動で最適に設定する技術
環縫いミシンの針糸、ルーパー糸を一針ごとに縫製に必要な糸量を繰り出す糸調子の技術です。押え高さ、メス幅、送りピッチ、縫い目の種類に連動して、繰出す糸量が可変し、最適な糸調子を自動で設定します。

空環カッター
ボタン操作で安全・簡単に空環をカットする自動空環カッター技術
家庭用ロックミシンの空環をボタン操作でカットする自動空環カッター技術です。縫製時に邪魔にならない回転刃を採用。また、回転刃に連動する可動式セーフティカバーの動きをセンシングすることで異物を検出し、誤って指などがカッター刃付近にあっても、刃部が直接触れない安全設計としています。
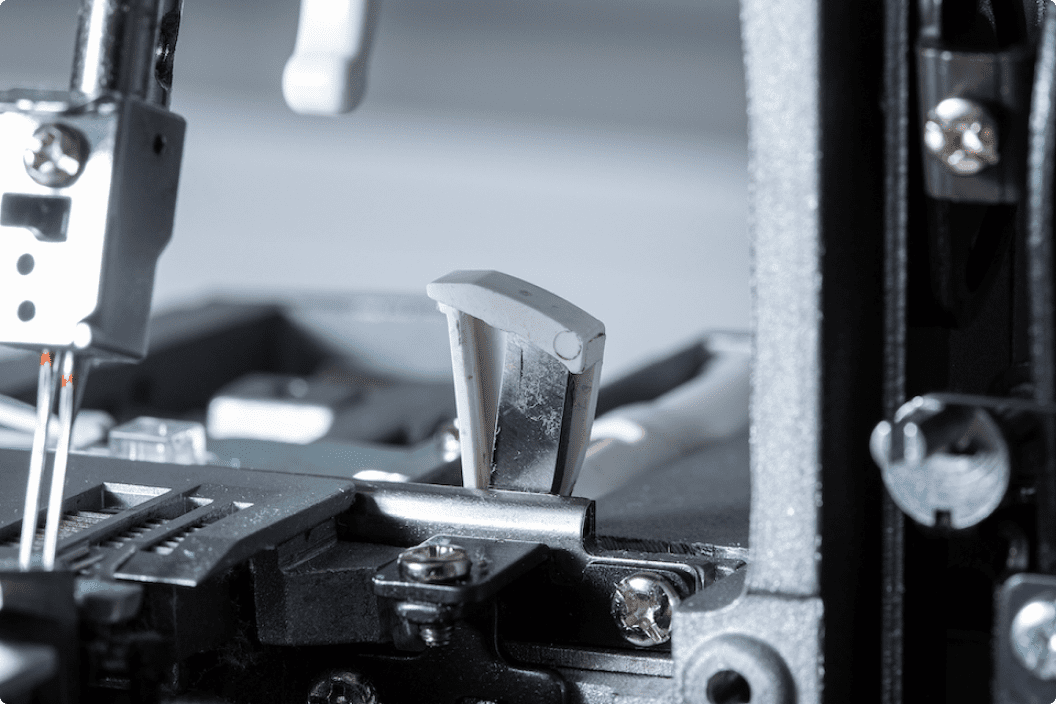
JUKIスマートステッチ
縫いスピードが変化しても一定の縫いピッチを実現
縫う方向を360度自由自在に転換しながら、ステッチ模様を入れるミシンに備わっている技術です。2次元センサを針板の表面に付けたことにより、布が動いた距離を測り、動いた距離に応じて、ミシンの回転数を変動させ、縫いスピードが変化しても一定の縫いピッチを実現します。

ボックス送り
縫い縮みや布ズレを防止
「四角」を描く送り軌跡にすることで、生地が送り歯に隙間なく接し、生地送りを安定化させた技術です。薄地・厚地の素材もスムーズに送り、極端な段部乗り越え縫いも容易にしています。カムの形状を特異にさせ、水平に送りストンと落とす極端な動きをすることにより、箱のような四角い軌道を実現しました。

自動糸調子
模様の種類に応じた上糸の張力を実現
上糸の張力を、縫い模様に応じて自動調整する技術です。振り幅、送り量から決定した圧力を、内蔵された縫い模様数351種類と文字模様のそれぞれに対して、上糸に最適な糸張力を与えます。専用のステッピングモーターを搭載することにより、糸調子カムの回転角度をデジタル制御しています。

フロートモード
押え上げ状態を認識する独自技術
押えをわずかに布から浮かした状態で縫うことができる技術です。エンコーダにより押え高さを常に検知することで素材に合わせた0.1㎜単位での設定ができます。生地の間に綿を挟んで縫製する場合などの縫いズレを防止できます。

ピボット機能
ミシン作動・停止時に合わせた、独自の技術
縫いを一時停止した際に、針が生地に刺さった状態で停止し、押えを少し浮かせる技術です。エンコーダによる検出で生地の厚さに合せ、押えの高さ設定も変更できます。再スタート時は押えが自動で下がり、角縫いやカーブ縫いなどの際に、作業時間を短縮できます。

プラネットヘッド
回転型ヘッドで、小型部品の高速搭載を実現
回転型ヘッドのことで、部品の吸着・装着がコンパクトなため、高速搭載を可能にするロータリー技術です。
吸着部品を順次回転させるため、部品認識の効率がよく、タクト短縮につなげることができます。また、吸着順に装着するため、不良発生時の解析がしやすく、ノズル※を増やすことも可能です。
- ※ノズル:部品を吸着&装着する部品のこと

匠ヘッド
部品に応じて、認識高さを可変
インラインヘッドのことです。搭載する部品の高さに応じてヘッドを固定したままレーザ認識装置のみを上下動させる技術です。部品認識・搭載を最適な高さで行うことができ、高速搭載を実現します。これにより部品の高さに応じたヘッド仕様が1種類となり、高速性と汎用性の両立を実現します。

ヘッド交換
単体機の中で2種類のヘッドを交換する技術
プラネットヘッド(ロータリーヘッド)と匠ヘッド(インラインヘッド)を生産内容に応じて交換できる技術です。生産体系が大きく変わっても容易にフレキシビリティーのあるライン構築ができます。

高精度ピン認識技術
異形部品挿入の画像認識
挿入部品のリードを3次元画像処理することでピン部分のXYの位置、長さの違うボスやピンなどを一括認識できる技術です。ラフな形状が多い部品へも画像認識ができ、正確な位置決めを実現します。
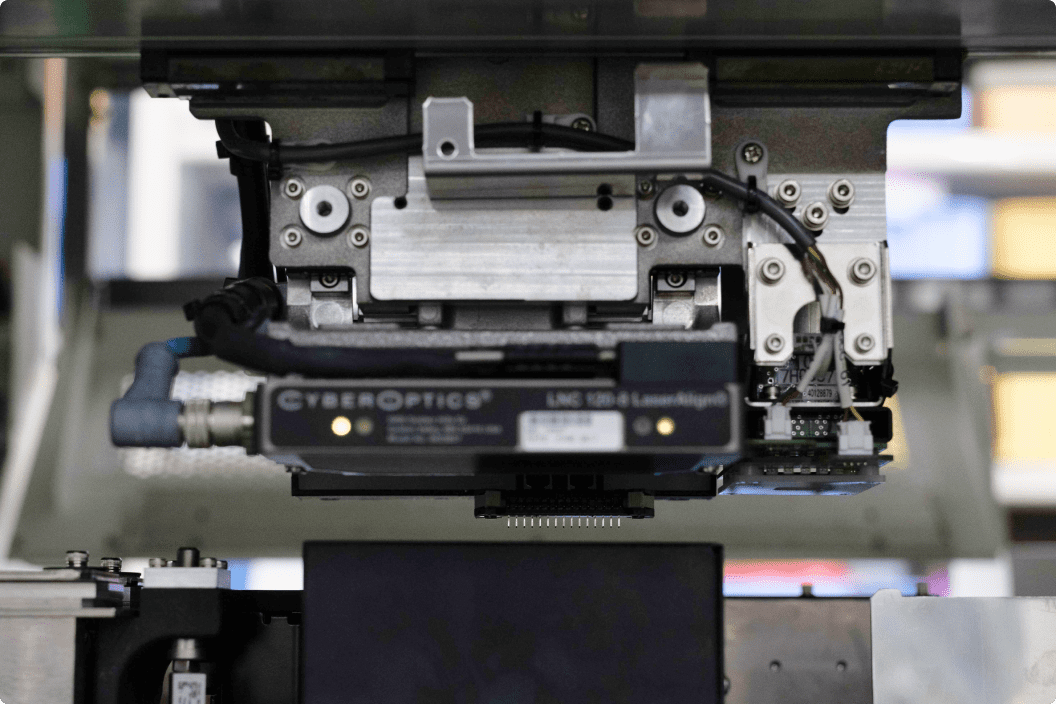
レーザ認識技術
部品吸着前後、搭載前後で部品の状態をビジョン認識
高い分解能をもつフライング認識ユニットをヘッドに装備し、透過光による部品シルエットを読み取ることで、部品の位置と角度を演算する技術です。演算はフライングビジョンによりXY移動中に即座に行うことができ、タクトタイムを高速化できます。
搭載直前までの部品の吸着状態をモニターできるため、吸着、搭載時の部品の有無、正常吸着、正常搭載を確認でき、また搭載後の不良の有無を検知できるため、即座に不良原因が判り高い生産品質につながります。

3D画像認識(検査機)
DLP方式投影装置で鮮明に撮像
投影・撮像を駆使し3次元で検査する技術です。ヘッドユニットにDLPプロジェクターを4方向に配置し、32パターンの縞模様の光を部品に投影することにより測定精度が向上できます。

画像認識技術
専用カメラと多様な認識方法で、安定した部品認識を実現
部品認識専用カメラと多様な照明方式により、小型チップからIC部品や大型・異型部品まで撮影することで、部品の位置決めと不良がないかを判定します。部品を同時に下と横から異なる波長の照明を照射することで、下からの画像処理でXY座標を、横からの画像処理で部品の厚み寸法を計測でき、高速化が可能となります。

部品ベリフィケーション(CVS)
生産稼動開始前(マウンタ)に部品の電気特性を検査する技術
生産開始前や部品切れが生じた後の生産再開時に、搭載する部品の電気特性(抵抗値、コンデンサ容量、部品極性)を検査する技術です。外観検査機では判定できない部品検査が行えるため、部品・リールの誤装着を防止することができ、部品の誤搭載を根絶できます。
