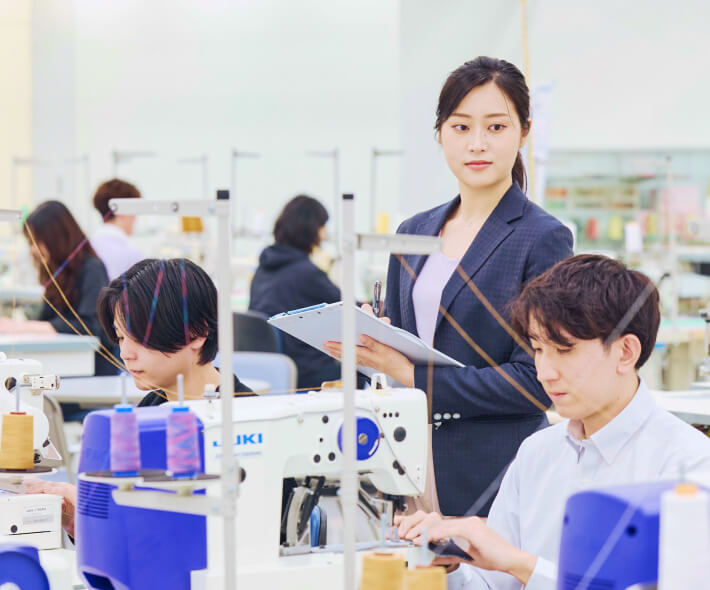
売って終わりじゃない。
現場の困りごとを知り、解決までフォローし続けるのがJUKI
世界中のものづくりの現場で、お客様のお困りごとを解決していく。
そんなJUKIのビジネスを体現しているような部署があります。
それが、縫製機器&システムユニット スマートソリューションカンパニー(以下SSC)です。
ここで働く社員のエピソードを通じて、JUKIがどんな風にお客様のお困りごとを解決しているのかをご紹介します。
INTERVIEW
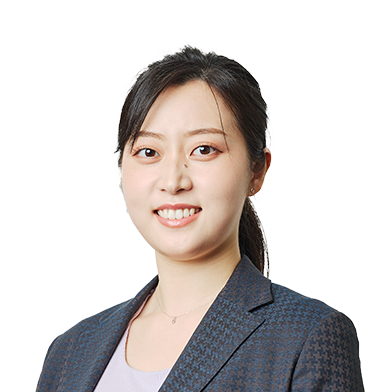
スマートソリューションカンパニー
営業2022年 新卒入社
家政学部被服学科卒。アパレルの知識を活かしつつ、社会に役立つ実感が持てる仕事がしたいとJUKIを志望。ゼミの教授や親の「間違いない会社」という言葉にも背中を押された。面接で、「洋服のつくり方を学んできたのなら、工場のオペレーターさんと同じ目線で話せる。それがすごく重要になる仕事」と言われ、自分がやりたいことだと感じ、入社を決意。
半世紀以上にわたって、縫製工場の近代化を進めてきた
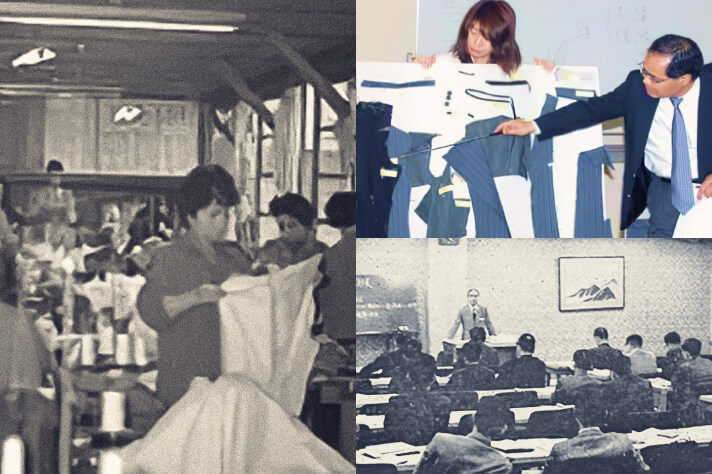
JUKIが工業用ミシン事業を開始した1950年代当時、縫製工場の多くは家内工業的で、カンと経験に頼った生産・運営が行われていました。この状況を改善、データを基に科学的な管理を行うことを目的に、1959年に設立されたのが「縫製能率研究所」です。
同研究所は縫製生産システムを社内で独自に研究、その成果をもとに縫製工場の近代化を支援していきました。生産管理、IE(Industrial Engineering、生産工学)技術を用いた活動は、当時、縫製産業の未来を開く活動として書籍でも取り上げられるなど話題に。
また、同研究所が行ったコンサルタント的なビフォア・アフターサービスは、JUKI製品の満足度向上や、JUKIブランドの信頼に大きく貢献しました。
この研究所の活動を受け継いだのがSSC。
そして、このSSCに、2022年の入社以来在籍、第一線でコンサルティング活動を行っているのがR.Sです。
これまで5社ほどのお客様を担当。
「国内だけでなく、ヨルダンのお客様の担当になり、現地に出張したこともあります。(R.S)」
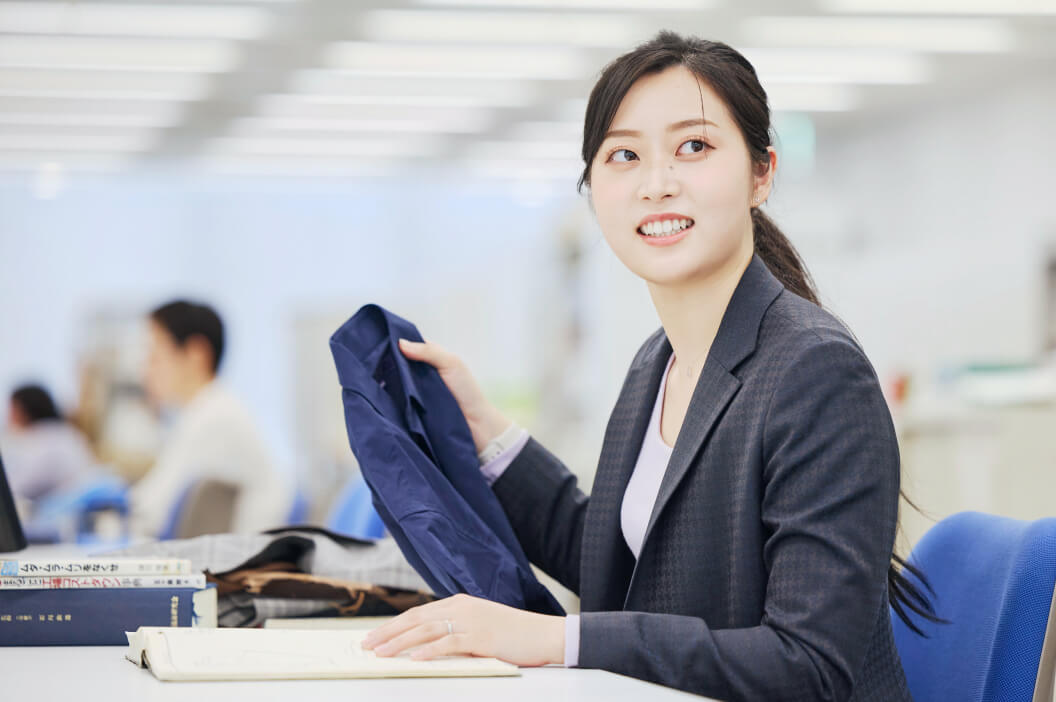
JUKIのノウハウが世界中のお客様に受け入れられているのかも。
すごい!
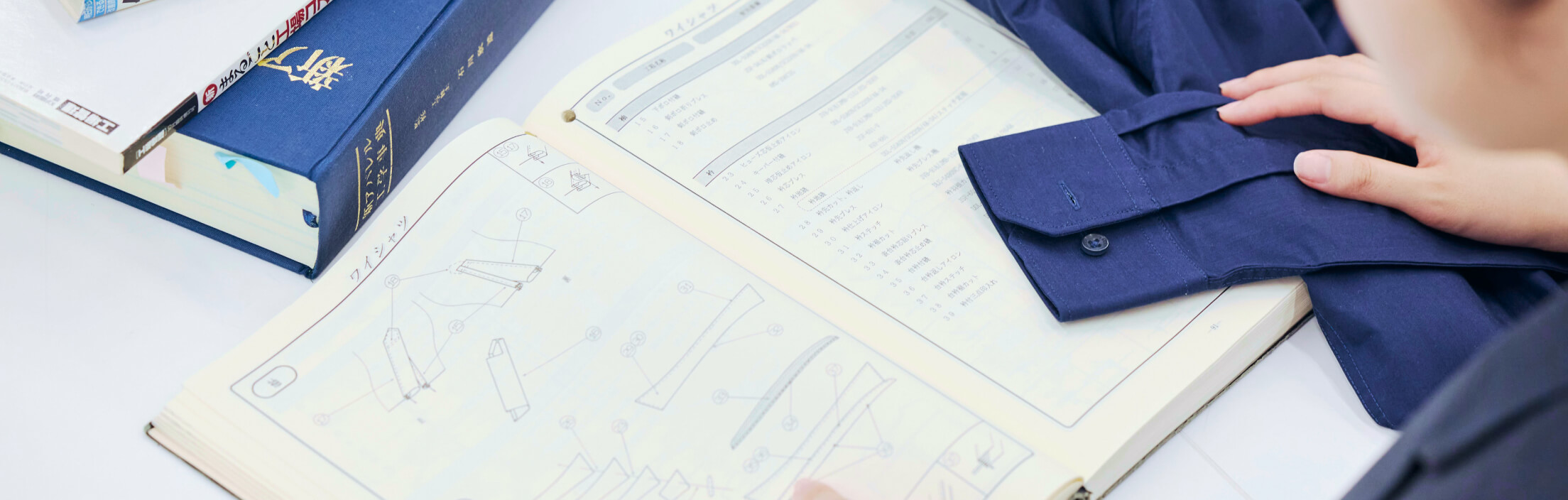
R.Sの所属するSSCでは、現在、縫製研究所が担ってきた次の3つの活動を行っています。
一つ目は「工場診断」。
縫製工場の現状を科学的に分析し、生産性向上の改善をご提案するもので、これまで国内外合わせて6,000社を超える実績があります。
「私が主に手掛けているのも、この工場診断です。(R.S)」
二つ目は、「プラント設計」。
縫製システムや生産量にあわせて最も合理的な使用設備を割り出し、効率的で発展性のある工場レイアウトを設計します。
そして、三つ目が「セミナーの実施」です。多彩なプログラムで、長年研究してきた生産性向上や課題解決の手法を紹介、お客様ご自身が自社の工場で実践できるようサポートするものです。
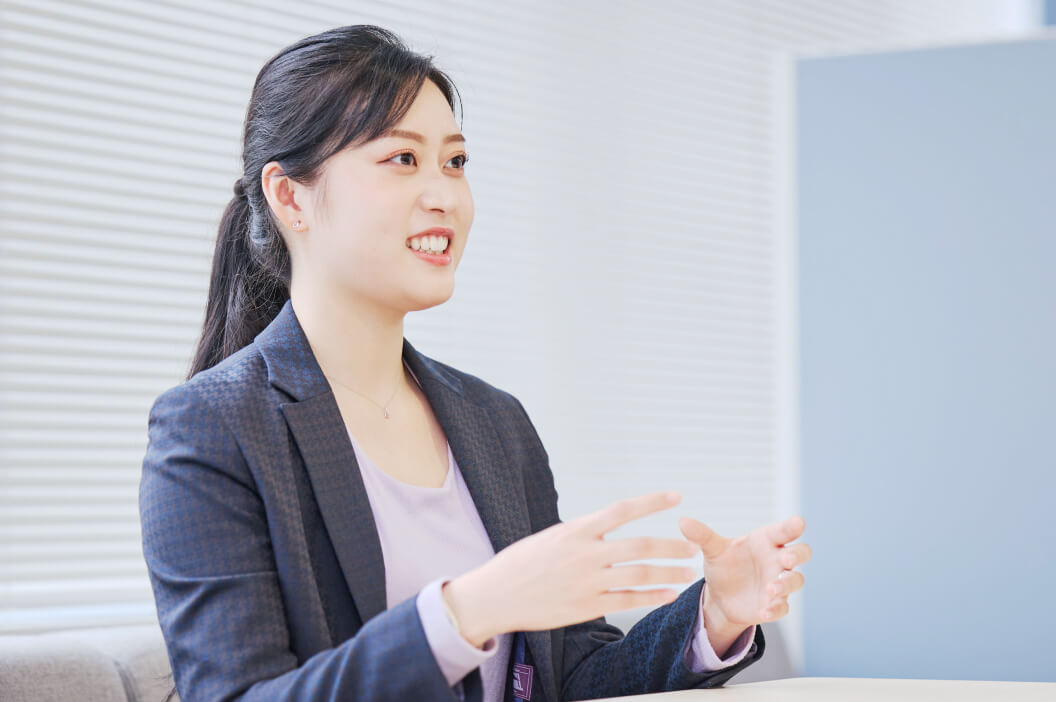
R.Sは2023年に、このセミナーに初めて参加しました。
「ご紹介する手法などは、基本的には変わっていないといいます。お客様、工場、あるいはその年によって、改善したいところや悩みも変わってくると思うんですけど、全部の悩みに変わらず適用できている!びっくりしましたね。(R.S)」
セミナーは、これまで国内外62,000人以上の方が受講。毎年、参加されるお客様もいます。
「工場の課題分析や解決手法だけでなく、そもそも縫製作業で何を一工程とするかとか、JUKIが定義したものもたくさんあるらしいんです。工場での縫製を考えるうえで基本中の基本となることをJUKIがつくり、それが世界中のお客様に受け入れられていく。すごいと思いましたね。(R.S)」
直接話を聞き、一人ひとりのスキルや工場の人間関係も把握
R.Sが主に担当している工場診断。お客様がJUKIを呼ぶ理由は、基本的にお困りごとがあるからだとR.Sはいいます。
「生産や製造に課題があるという点は一緒です。でも、つくっているものや規模は本当にまちまち。私がお邪魔した中でも、全員で10数名、工程も少ない工場から、6階建ての階全部に縫製作業をするオペレーターさんがいて、裁断から出荷に至るすべてを手がける工場まで、いろいろでした。(R.S)」
多品種少量生産あり、大量生産ありと生産方式もさまざま。当然、改善すべき箇所も、生産性が上がらない理由もそれぞれ違います。
そんな中、改善提案を考えていくには、データによる裏付けが欠かせません。
「縫製研究所からずっと使ってきた手法を使って、まず現状を把握。工場に出向き、「工程分析」「稼働分析」「時間研究」の3つの観点からデータを取っていきます。(R.S)」
現場でのヒアリングも不可欠です。班長、ライン長といった責任者の方々はもちろん、オペレーターさんにも話を聞き、個人の技術力や工場全体の人間関係なども把握していきます。
「1日の生産量とか数字だけを見て、単純に作業の速い人と遅い人を交代すれば平均的になるという解は導けます。でも、オペレーターさんに『こっちの方の作業できますか?』と聞いたら、『自信がありません。』って言われたり。それはそうですよね、得意不得意もあるし、こっちの人との方が仕事がしやすいとかありますから。だからこそ、データ上の改善だけでなく、実際に作業するオペレーターさんに寄り添うことを心掛けています。(R.S)」
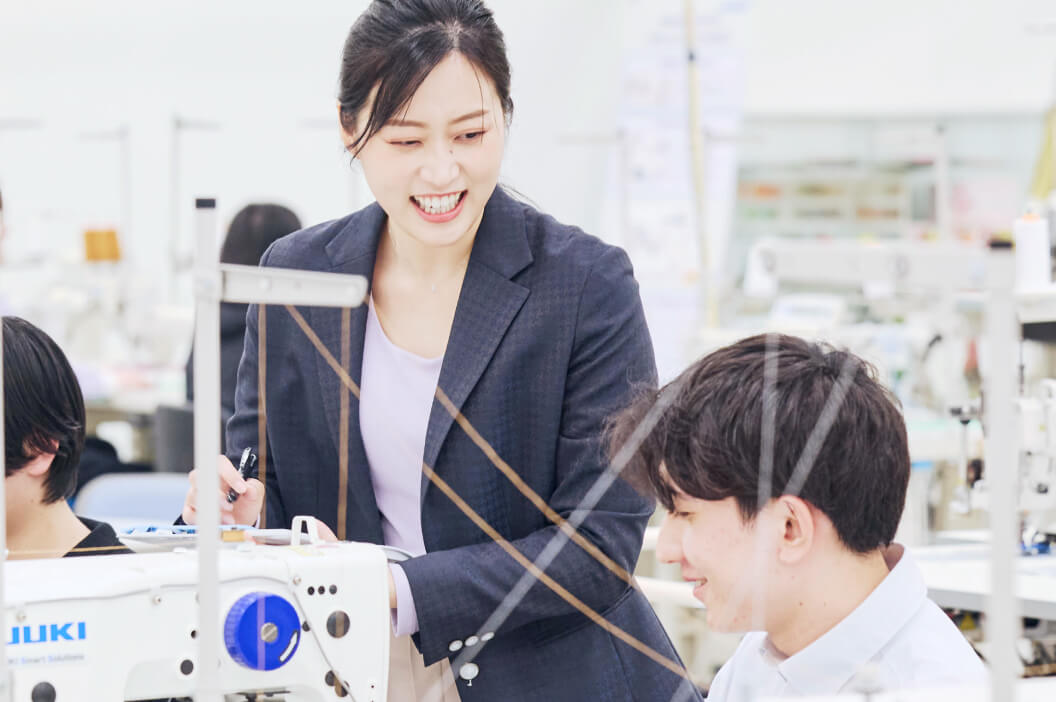
提案したことが継続され、成果が出ているときのうれしさ
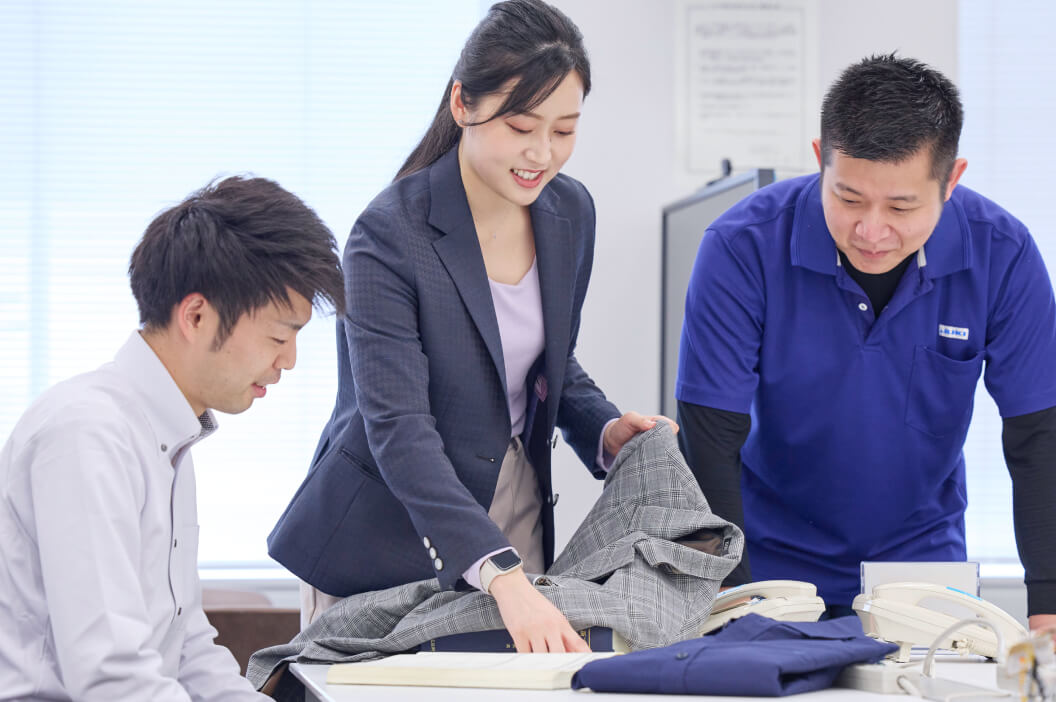
提案内容もさまざまです。お客様が目標とする生産枚数の達成というゴールは同じでも、その実現のために、オペレーターさんの動作を改善するのか、あるいは作業環境、作業配分を改善するのか、いろいろなアプローチを考えます。
改善策をまとめ、報告会で発表する際、現場の意見を取り入れることもよくあるとR.S。
「オペレーターさんから『JUKIさんから管理者に伝えてほしい』と言われて、例えば、ミシンが老朽化して現場が困っているので変えるべきなどの提案をすることもあります。ただ、どうしても予算が取れず見送りになることも。そういうときは、現場の思いを果たせない悔しさを感じます。私たちに託してくれたのにって。(R.S)」
また、調べ抜き、考え抜いて提案しても、あくまでそれはJUKIの提案。強制力はないので、その後、本当に提案を受け入れていただけるかはお客様次第です。
「だからこそ、提案を実践していただけるのが分かるとすごくうれしい。自分の提案が、今、目の前で行われているって。(R.S)」
例えば、オペレーターさんに動作の改善を提案しても、すぐには慣れないため効果はすぐに出にくいもの。
「そんな中で1年間続けていただき、しっかり成果が出ていたりすると、心からよかったって思います。(R.S)」
外部の人間だからこそ、提供できる価値もあるようです。
「現場で調査をしているとき、あるオペレーターの方の作業がすごく早かったので、『お手本として動画を撮らせていただいていいですか?』と言ったら、『私、お手本なの?』って。どうやら、生産量が上がらないのは自分のせいと思い込んでたみたいなんです。作業の動作とかって、私たちのような外部の者が客観的に評価、指摘しないと分からないこともあります。その方、『ありがとう、私、頑張る!』って、すごくやる気が出たみたい。よかったなって、心から思いました。(R.S)」
「お客様が楽になることが一番の目標」。カッコいい、Kさん!
R.Sには目標となる先輩がいます。
「ズバリ、Kさん。工場診断をメインにしてる一番年次が上の方なんですけど、ミシンも工場のことも詳しくて敵なし。何を聞いても詳しくて、難しい問題でもすごく納得いく解説をしてくださいます。(R.S)」
当然、お客様からの信頼も厚く、「Kさんに分析をお願いしたい」と指名が入るほど。お客様への気遣いも違うとR.Sはいいます。
「一緒にお客様先に行ったときに、Kさんが工場全体への挨拶を頼まれたんですね。で、『お客様の仕事が楽になることが、私たちの一番の目標です。そのために私たちは来ました」って。すごくカッコいいなあと。ミシンを買っていただいて終わりじゃなく、最後までフォローして、『楽にする』するとか、お客様のためであろうとする。それこそJUKIだよなって。(R.S)」
買ってくださったお客様の工場をよりよくする提案をすることが、JUKIの付加価値と言い切るR.S。
だからこそ、まずは現場に行くことが大切だといいます。
「現場に実際に行かないと、お客様の困りごとはわかりません。ミシンを使う方が本当はどう思ってるのか、どうフォローしてほしいのかも分かりません。(R.S)」
そう考えるのは、R.Sだけではないようです。
「先輩も、お客様に呼ばれたら海外でもすぐに駆けつけるし、自分から訪問したりもする。お客様をフォローする姿勢は本当に学びたいですね。しっかり受け継いで、これからも私もお客様の目線でフォローをしていきたいです。(R.S)」
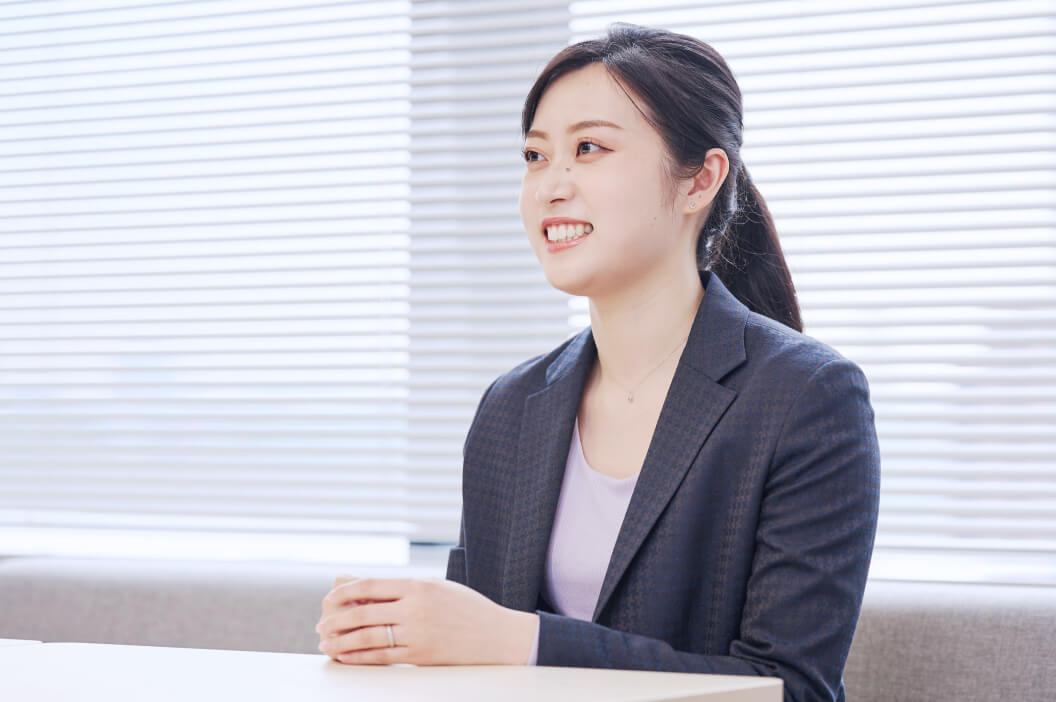